Automating the gigafactory
The UK could have 10 gigafactories by 2040, each producing 20GWh per year. Automated systems, sensors and robotics will support the EV battery industry in boosting productivity, enhancing efficiencies and reducing downtime. By Rich McEachran
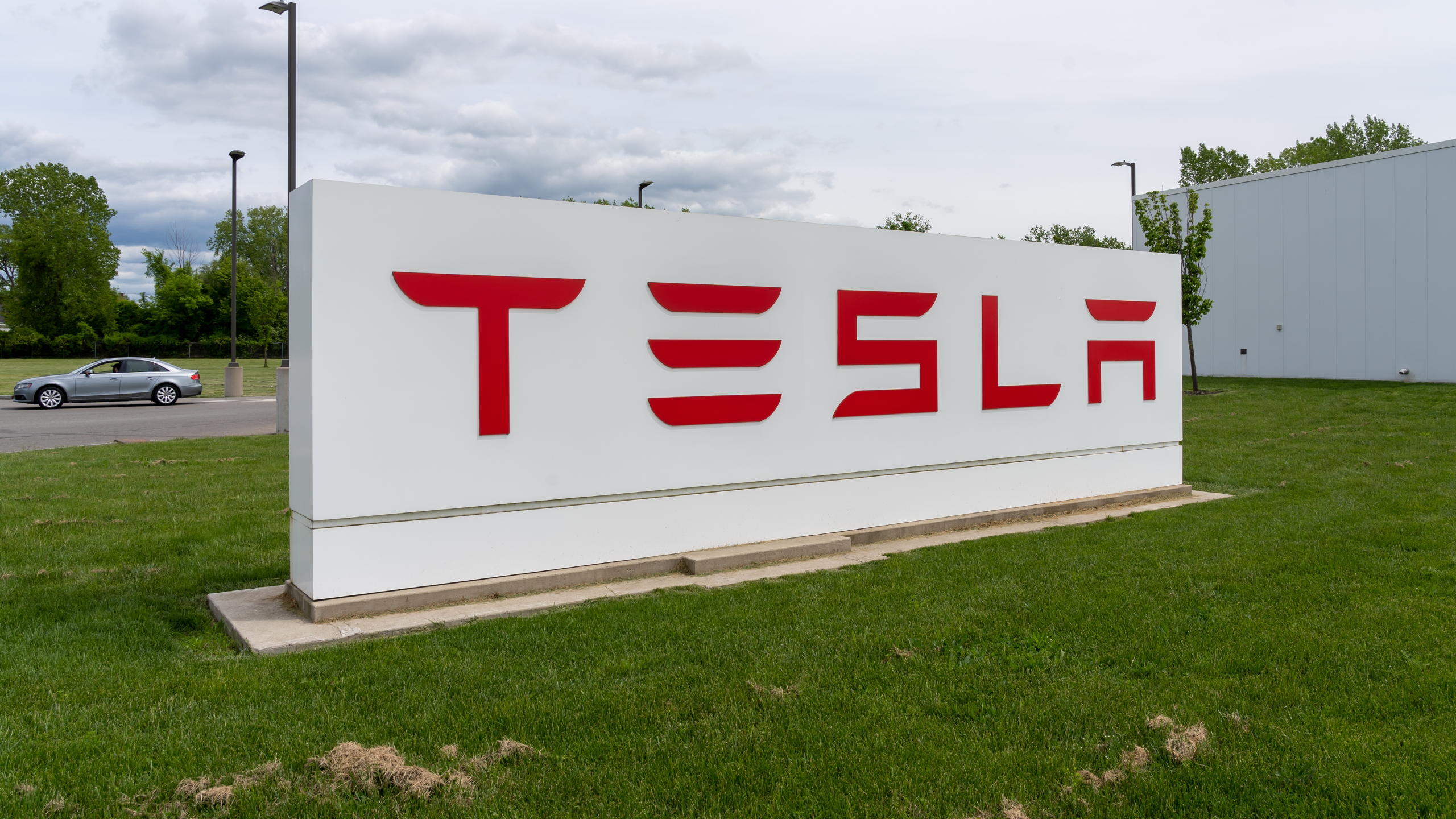
As demand for electric vehicles (EVs) continues to accelerate, so will the demand for the batteries needed to power them. Gigafactories have been touted as the answer to the supply-demand challenge and automation could be key to ensure that batteries roll off the production line efficiently.
Back in 2013, Elon Musk touted the potential of the gigafactory, a new Tesla battery production facility that would have recycling capabilities built in, where “oldpacks would come in one side and get reprocessed as new packs”.
Musk claimed that the “really giant facility” would be equivalent “to all lithium-ion production in the world in one factory”.
Fast forward a decade and Tesla has four gigafactories across the US, one in Berlin and another in Shanghai. A seventh is being built in Monterrey, Mexico.
Gigafactories are springing up elsewhere as more countries look to reduce their reliance on China and onshore their battery supply chains. In May, France opened the first of four gigafactories planned for the north of the country. The production line at the facility – a joint venture between French utility TotalEnergies and carmakers Mercedes and Stellantis – will have an initial capacity of 13GWh per year, although this will eventually be scaled up to 40GHw.
Last year, the Faraday Institution forecast that there will be five and 10 gigafactories in the UK by 2030 and 2040 respectively. On the assumption that each facility will produce 20GWh per year of batteries, the UK will be able to meet 10% of the projected 10,000GWh per year of European production capacity in 2030.
However, the institution warned that the UK will have to act quickly to avoid being left behind in the EV manufacturing race. This means the industry will have to utilise the latest technology to gain a competitive edge, including Industrial Internet of Things, data-driven optimisation, materials analysis, continuous simulation and, perhaps most importantly, automation.
The importance of automation
“Gigafactories might be touted as an answer to meet global battery demands, but they require implementation of automation to be efficient,” says Philip Meek, CEO of Liacon, which operates one of Europe’s largest lithium-ion battery factories in Ottendorf-Okrilla near Dresden, Germany.
The German battery manufacturer, owned by Canadian firm Trion Battery Technologies, unveiled a 12V lithium-iron-phosphate (LFP) battery in May to replace 12V lead-acid batteries. The latter can still be found in some electric vehicles – Tesla started switching away from them in 2021 – as they can be relied upon for standby power. The problem with lead-acid batteries, though, is that they are cumbersome and will need replacing after a few hundred cycles. Liacon’s LFP battery can last up to a few thousand cycles, it’s claimed.
Meek goes on to explain that, at the most basic level, automation is useful when it comes to battery assembly. Rather than let human errors slip in, workers can programme automated systems to carry out the assembling more quickly and more efficiently.
“Tasks like cell stacking and testing, as well as the coating of electrodes, are highly repetitive. These are steps that require meticulous attention to detail,” he says.
‘The UK’s engineering and manufacturing workforce can gain a competitive edge over other countries’
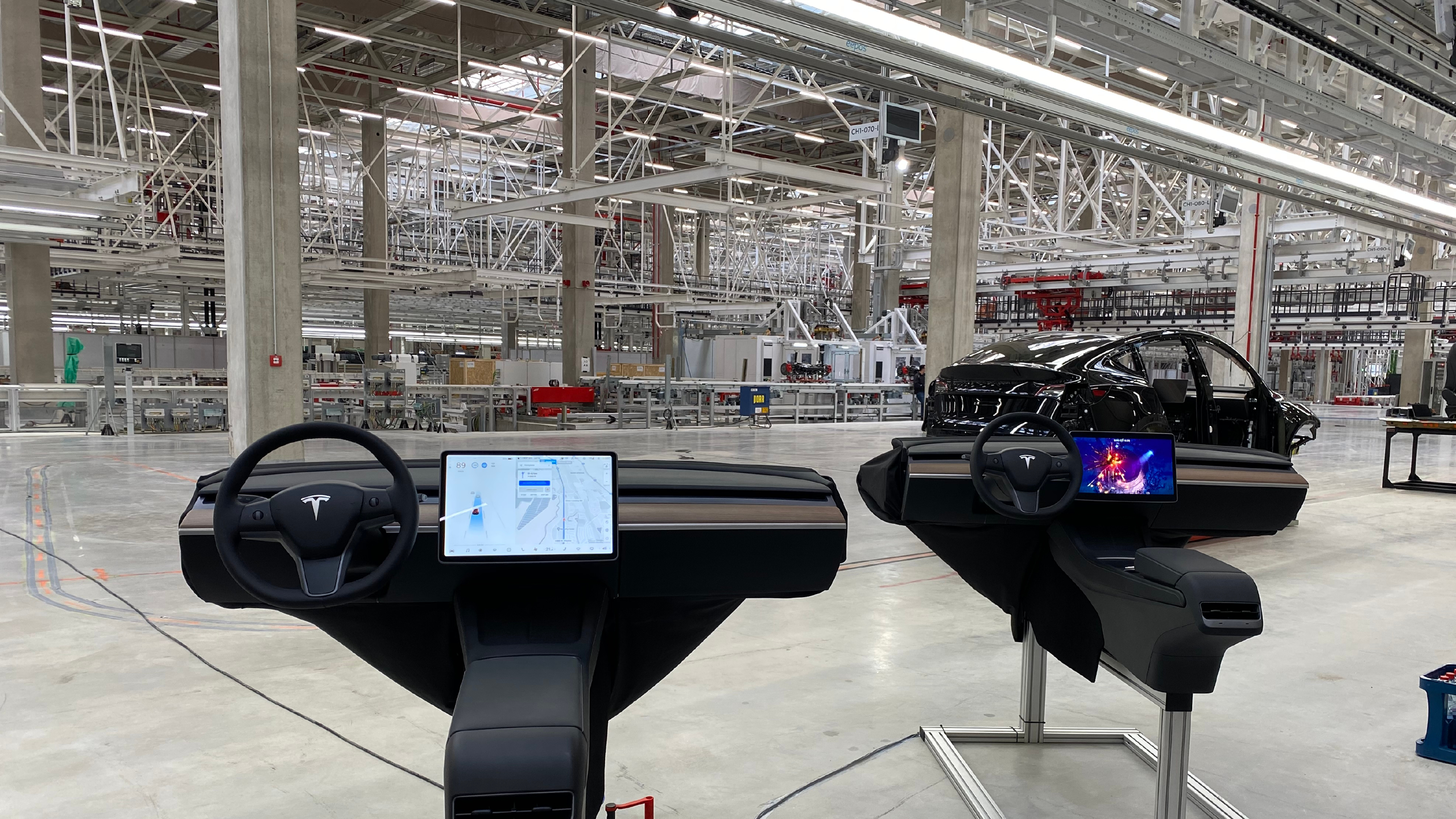
Keeping on top of quality control
Although some might assume that automation is mainly about having the most sophisticated software installed, the right hardware is just as important. Robots will whiz around in the gigafactories of the future, moving components, materials and heavy loads from A to B. “Gigafactories will need to make sure that parts are where they need to be, when they need to be,” Meek continues.
Meanwhile, versatile and dexterous robotic arms that can grasp and manipulate objects will play a role in quality control. When combined with sensors, the impact of robotic systems can be transformative. The sensors can be used to monitor and ensure that there’s uniformity in the cathode and anode thickness during production, and robotic arms can be used to remove them from the production line, for example. This prevents cell waste and can improve cell performance.
Once battery cells arrive at the final assembly point, machine vision – where cameras combine with software to analyse hundreds of images a second – can be utilised to verify that all specifications are met. Machine vision can spot defects that are almost invisible to the human eye.
“Sensors pick up defects or anomalies before the products are shipped out to customers, lowering the risk of faulty batteries and EV makers having to issue recalls,” says Meek.
Machine vision can also double-check the alignment and height of battery packs to ensure precision.
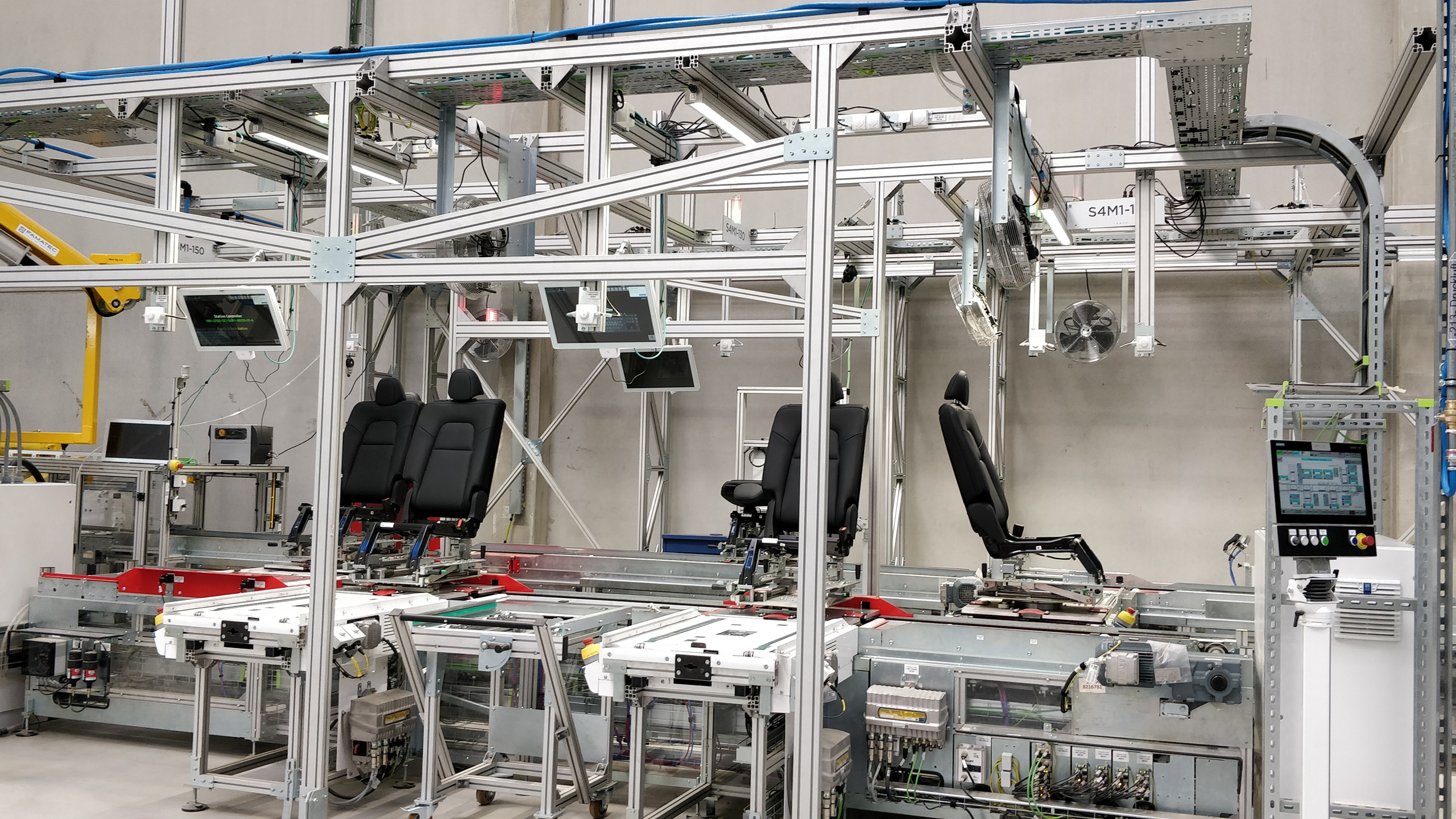
Automation won’t eliminate the need for high skill sets
With all the vast volumes of data being generated by the sensors and connected devices on the factory floor and by robotic systems, automated systems will be needed to monitor the entire manufacturing ecosystem in real time, identify areas of improvement and flag any areas of concern.
“Machine learning algorithms can be deployed to analyse the data and pick up patterns, and predict upcoming maintenance issues like parts replacements,” explains Meek.
“This way, teams can proactively act on the issues before equipment starts breaking down, which could potentially shut down production for weeks.”
While automation’s role will be elevated further as artificial intelligence continues to mature, powered by the latest advanced semiconductors, human workers aren’t on the verge of being made obsolete. In fact, the need to automate battery production will call for talent with the right industrial skills to turn the data leveraged and turn it into actionable and tangible insights.
If the EV industry wants to successfully meet GWh production capacity demand in the future, then it’ll need to ensure it has the right infrastructure and support network in place to attract and retain the right talent.
According to the Faraday Institution’s gigafactory outlook report mentioned earlier, higher skill sets will be needed for the technical nature of cell manufacturing and to help gigafactories to use the latest technologies and compete for production capacity. Furthermore, gigafactories that plan on doing their own research and development would need support from well-qualified engineers and PhD scientists, the reported pointed out.
“The UK’s engineering and manufacturing workforce can gain a competitive edge over other countries through the provision of a national training curriculum that will ensure the right skills are delivered at the right time.” stressed Matt Howard, the institution’s chief strategy officer.
The right talent with the right skills won’t guarantee that the EV industry won’t have problems in meeting demand for EVs in the future, but it’ll put gigafactories in the best position possible to boost productivity, enhance efficiencies and reduce downtime.
As Meek puts it: “Gigafactories that follow these automation techniques will experience a surge in production capacity, churning out high-quality, reliable batteries that meet the world’s increasing demand.”
You're reading a brand new digital publication from the team at Professional Engineering, made exclusively for IMechE members and available on all devices. We'd love your feedback: let us know what you think at profeng@thinkpublishing.co.uk