THE DEFINITIVE GUIDE TO 3D PRINTING
WITH THE LATEST NEWS FROM FORMLABS, XOMETRY AND MORE
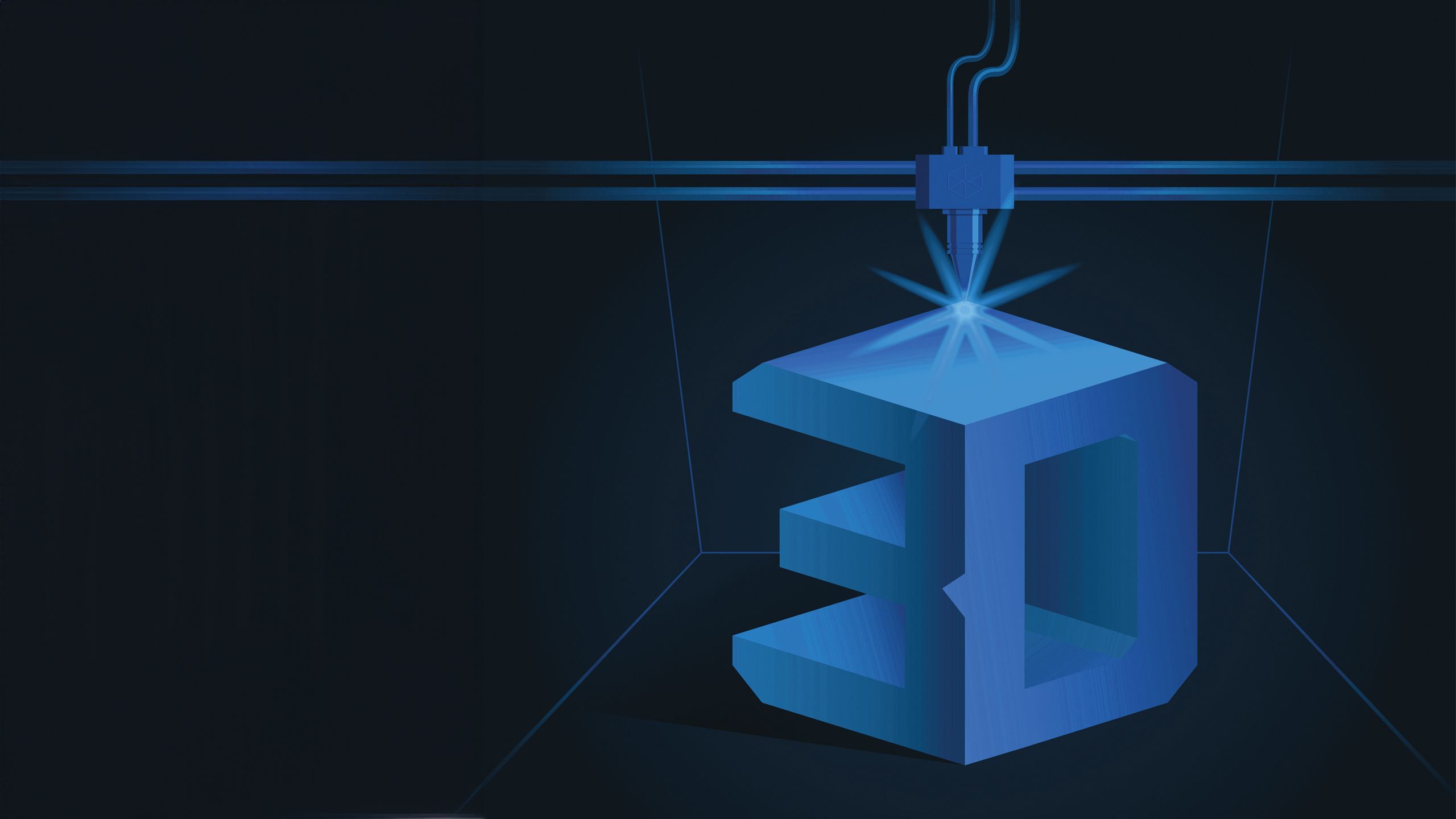
3D PRINTING FOR MECHANICAL DESIGN
3D printing, or additive manufacturing, has become a game-changer in the world of mechanical engineering. It empowers engineers to create prototypes, test parts, and produce custom components with remarkable flexibility. However, the multitude of 3D printing technologies available can make the choice overwhelming. In this article, we’ll delve into the key factors that influence your decision-making process, including material selection, accuracy, speed, cost, and complexity. By understanding these factors, you can make an informed choice that aligns with your mechanical design requirements.
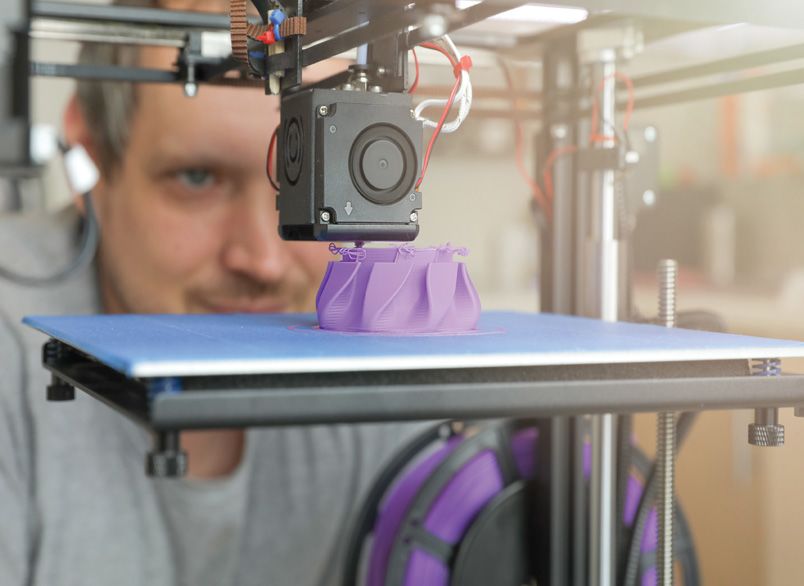
Mechanical engineer creating 3D printed part
Mechanical engineer creating 3D printed part
Material Properties
Material selection is your first critical consideration when choosing a 3D printing technology. Different 3D printing technologies are compatible with specific materials, each with its unique properties like strength, flexibility, durability, and resistance to environmental factors. For instance, Fused Deposition Modeling (FDM) commonly uses thermoplastics, while Selective Laser Sintering (SLS) can work with metals or polymers. It’s imperative to opt for a 3D printing method that can handle the material essential for your design, ensuring it meets the mechanical properties your project demands.
Accuracy and Resolution
Another crucial factor is the accuracy and resolution of the chosen 3D printing method. Accuracy refers to how closely the printed part matches the digital model, while resolution relates to the level of detail and surface smoothness. Different 3D printing methods offer various levels of accuracy and resolution, which depend on factors such as nozzle size, layer thickness, and movement precision. For instance, Stereolithography (SLA) utilises a laser to cure liquid resin, resulting in high accuracy and resolution. However, this method may require additional post-processing, like washing and curing, to improve mechanical properties.
Speed and Efficiency
The speed and efficiency of 3D printing are paramount considerations. Speed indicates how quickly the 3D printer can produce a part, while efficiency pertains to the amount of material and energy consumed. Speed and efficiency vary across 3D printing methods due to design complexity, part size, and the quantity of parts to be printed. For example, Direct Metal Laser Sintering (DMLS) uses a laser to fuse metal powder, making it capable of creating intricate and dense parts. However, it may consume more time, material, and energy compared to other methods.
Cost and Availability
The cost and availability of a 3D printing method are factors that deserve careful consideration. Cost encompasses the initial investment, material costs, maintenance, and post-processing expenses. Availability concerns of how accessible and user-friendly the 3D printer is, whether in-house or through a service provider. Different 3D printing methods come with distinct cost structures and availability profiles. For example, Binder Jetting is an economical method that employs a binder to bond powder particles, making it more affordable and widely available. However, it can produce parts with reduced strength and increased porosity.
Complexity and Functionality
The complexity and functionality of a 3D printing method are integral to the decision-making process. Complexity refers to how well the 3D printer can handle intricate shapes, overhangs, supports, and internal features. Functionality assesses the extent to which the printed part can fulfil its intended purpose, whether it involves mechanical, electrical, or thermal functions. Different 3D printing methods exhibit varying capabilities and limitations in these regards. HP Multi Jet Fusion, for instance, is capable of printing multiple materials with distinct properties in a single part, enabling the creation of functional components with embedded sensors, circuits, or actuators. However, it may necessitate more calibration, alignment, and integration compared to other methods.
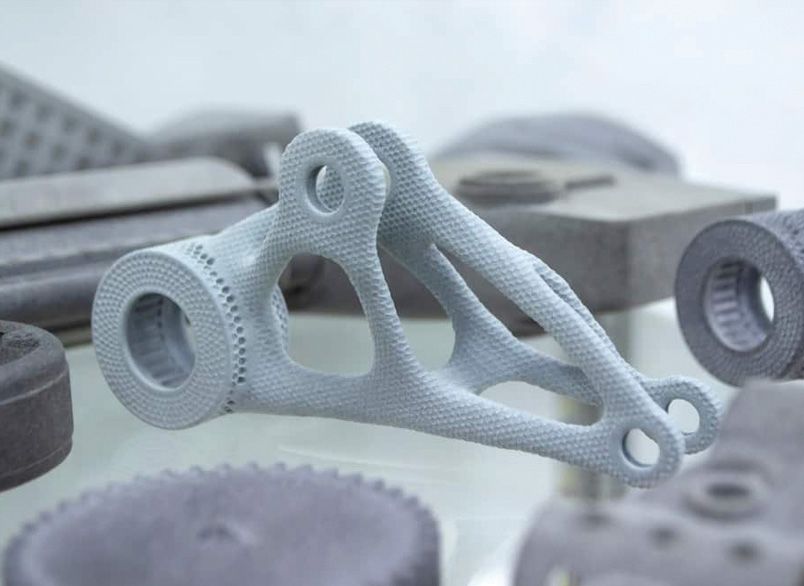
A complex HP MJF 3D printed part
A complex HP MJF 3D printed part
Start using 3D Printing for your next mechanical project
The choice of a 3D printing method for your mechanical design project should be a well-informed decision, guided by material compatibility, accuracy, speed, cost, complexity, and application-specific requirements. By carefully considering these factors, you can ensure the success of your mechanical engineering endeavour. Thanks to this cutting edge technology that is constantly evolving, Mechanical 3D printing enables the production of a batch of parts that are traditionally made of many components, reducing assemblies and welding steps, enabling you to produce products faster and ultimately saving time. Whether you’re producing prototypes, testing parts, or creating custom components, the right 3D printing method will be your key to success.
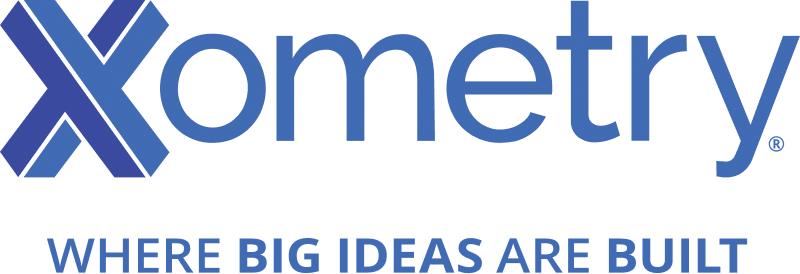
Xometry specialises in fast, reliable, and highly accurate 3D printing services of any quantity, precision, complexity, and required delivery time, we always have the manufacturing capacity to deliver your project. Head to Xometry’s instant quoting platform to upload your models and receive a quote in seconds, absolutely free.
REVOLUTIONISING 3D PRINTING WITH AFFORDABLE, PURE SILICONE
Silicone elastomers are versatile materials with high-performance properties making them attractive for a wide range of applications, from consumer products to medical devices, to industrial parts for automotive and manufacturing sectors. There are several processes for manufacturing silicone parts, including casting, injection moulding, and compression moulding. These techniques have design limitations and typically involve reduced design flexibility, long lead times, and high costs. Because it eliminates tooling, reduces labour, and improves flexibility, 3D printing is a powerful solution to help alleviate these challenges. Formlabs is transforming the industry by launching the first accessible 100% silicone printing resin, Silicone 40A Resin
End-use parts production
HGM Automotive Electronics is a specialty manufacturer that designs and supplies leading-edge electronic systems for automotive aftermarket use. Because they work with vintage cars, connectors and other electrical components become challenging to find as the original production of these items phases out.
Soft silicone is commonly used for automotive connector seals. The options for producing these parts are limited. Injection moulding is expensive for low-volume production, and traditional silicone casting is time-consuming. HGM Automotive turned to 3D printing for prototyping and low-volume production because it is the best option to fabricate parts on demand, in house.
With the introduction of Silicone 40A Resin, Guy Cardwell, Director of Research and Development at HGM Automotive Electronics, says they found “exactly the right stuff.”

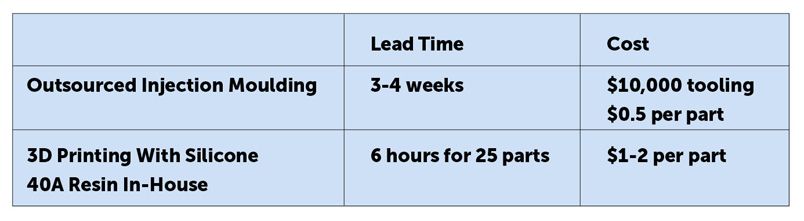
HGM Automotive succeeded with electrical connectors and therefore explored making custom seals. These seals are hard to find and usually of a low quality when available. Developing them was a challenge due to the lack of a suitably pliable elastomeric material. They considered using an injection mould with soft urethane but the downside is that this mould would cost between £5,000 and £8,250 just to get started. The cost would be justified if they needed 10,000 of these parts, but the reality is a volume between 100 and 1,000 pieces a year. Moreover, once the mould is made, design changes are almost impossible.
For a production volume of 100 units of connector seals, HGM Automotive reduced their costs by 98% and their lead time by 90%.
Cardwell adds: “I remember just handing some sample parts out to the various employees in the company and everybody's jaw just dropped, ‘Wow, how did you do this?’ So, it's exciting for us as a material. And you don't know until you actually use it, to really understand what the future applications are going to be, but I don't anticipate we're going to stop with connectors. There's going to be a bunch of other stuff we do with this. There's just no question in my mind.”
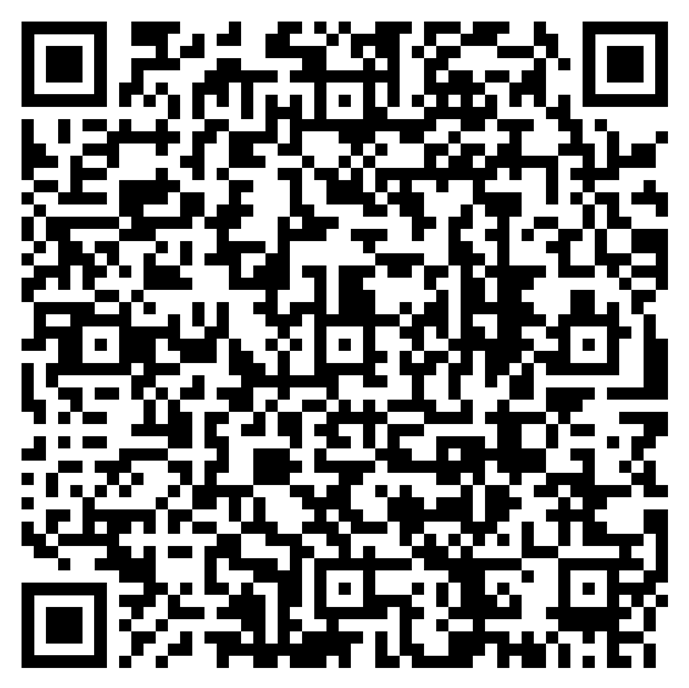
Dorman Products, a manufacturer of aftermarket automotive products, used Silicone 40A to make custom gaskets: reducing lead time from 2 weeks per set to only 3 hours. To find out more about their success story, and further possible applications with Silicone 40A, scan the QR code.