AUTOMOTIVE
REMODELLING MOTORS
Removing the need for magnets and rare-earth materials in making motors could deliver electric vehicles that are more sustainable.
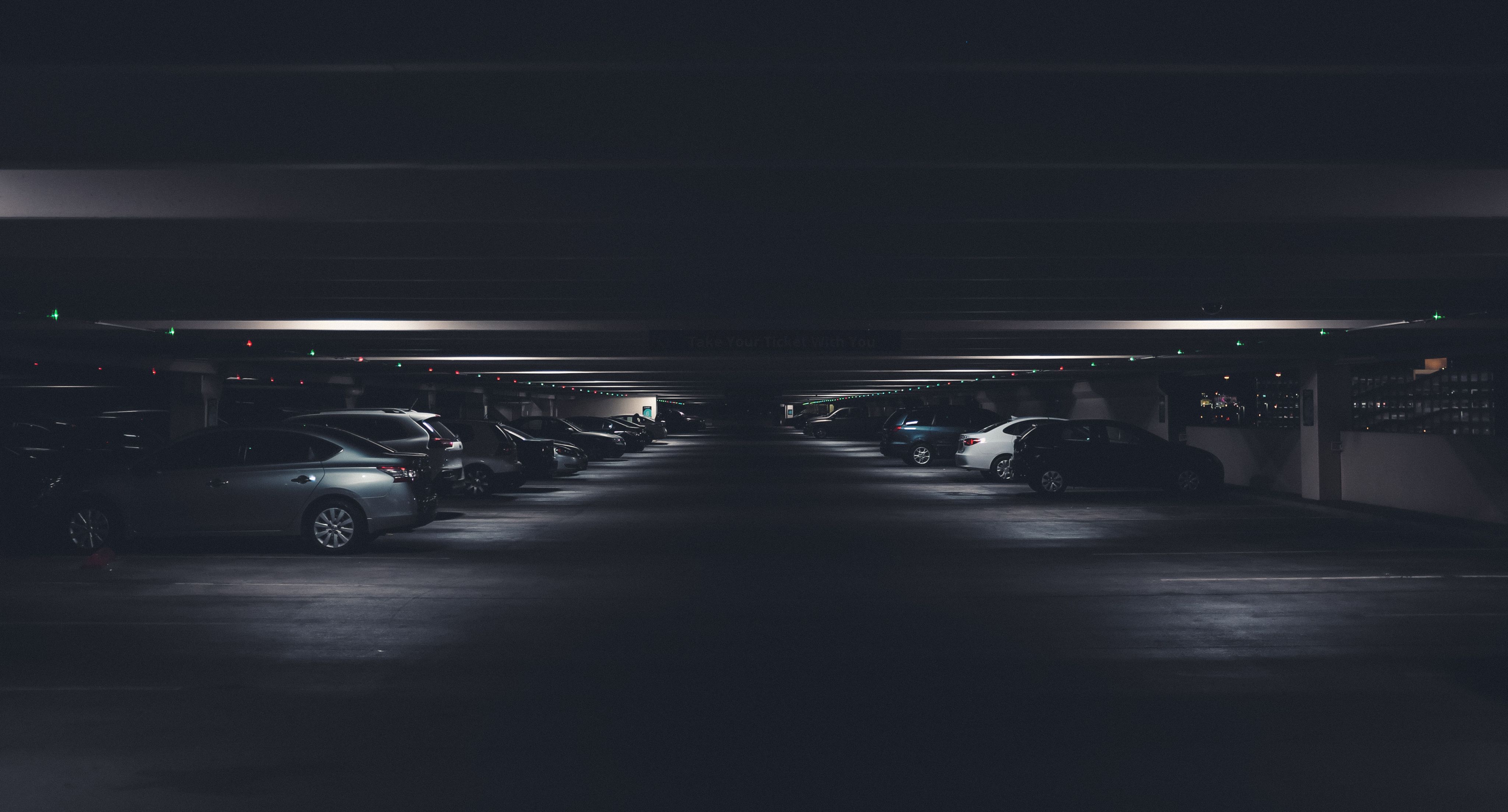
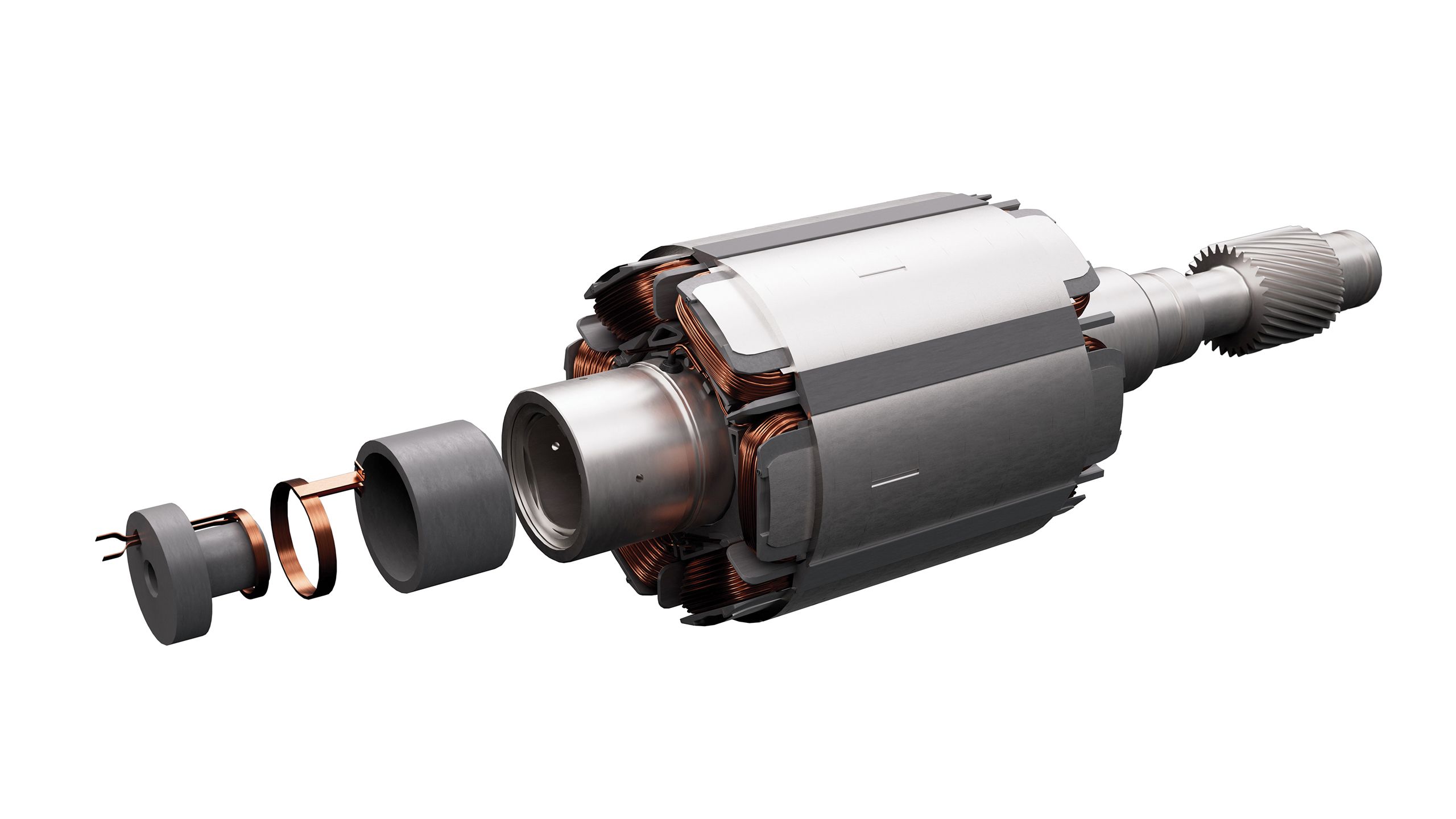
The automotive sector is grappling with how it can reduce its impact on the environment. Moving away from combustion technology is only part of the puzzle because, although it means burning fewer fossil fuels, electrification creates new issues.
Sourcing the materials to create electrified vehicles, particularly in the battery packs, isn’t a clean process, and also opens the door to human rights issues and geopolitical tensions. Improvements are being made, new technologies are making batteries better, and over the next decade a new generation of cells could make them better still.
But while the battery is arguably the biggest challenge to sustainability it isn’t the only area of electrified vehicles that needs to be addressed. The motors that drive EVs also pose problems.
Permanent-magnet synchronous machines (PSM) is the technology most frequently used in EVs, but they are based on magnets which require rare-earth materials for their production. And using anything with rare in the name isn’t good.
New approaches
Tier Ones are investing in new approaches that could help reduce the environmental impact of motor technology by removing the magnets and rare-earth materials.
Magnet-free technology isn’t necessarily new, with separately excited synchronous motors (SESM) concepts already in the public sphere, but ZF thinks it’s developed a technology that could increase the benefits further by making them more sustainable and compact without any power or torque losses compared to traditional magnet motors.
ZF’s I2SM (In-Rotor Inductive-Excited Synchronous Motor) transmits the energy for the magnetic field via an inductive exciter inside the rotor shaft. In addition to eliminating rare-earth materials in a compact and powerful package, the I2SM eliminates the drag losses created in traditional PSM motors. This enables better efficiency in certain modes such as long motorway trips at high speed.
‘ZF thinks it’s developed a technology that could increase the benefits further by making them more sustainable and compact’
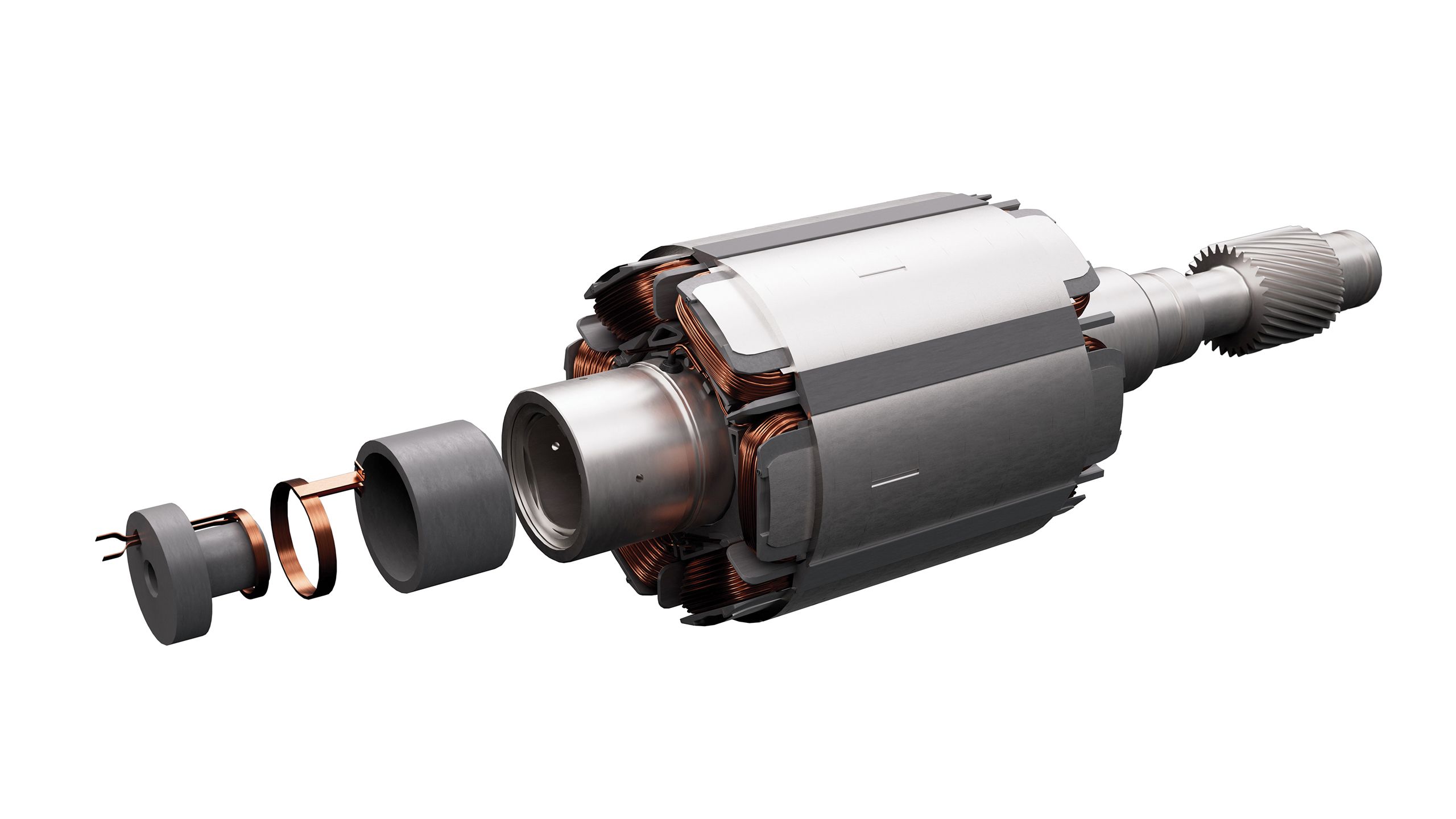
To ensure that the magnetic field in the rotor is built up by current instead of magnets, conventional SESM concepts require sliding or brush elements, forcing compromises: a dry installation space that isn’t accessible for oil cooling and with additional seals. That increases space axially by 90mm or more. As a result, manufacturers generally cannot flexibly vary between PSM and SESM variants in their model planning without additional effort.
In order to offer the advantages of separately excited synchronous machines, ZF has increased torque density thanks to an innovative rotor design. The space-neutral integration of the exciter into the rotor means that there are no axial space disadvantages. In addition, an increase in power density in the rotor leads to an improvement in performance.
Coils are key
The key to ZF’s magnet-free technology is that energy is transferred inductively, without mechanical contact, into the rotor, generating a magnetic field by means of coils. That means the I2SM motor doesn’t require any brush elements or slip rings. There’s also no need to keep this area dry using seals. As with a permanently magnetised synchronous motor, the rotor is cooled by circulating oil. Compared to common separately excited synchronous motors, ZF’s technology requires up to 90mm less axial installation space. But in terms of power and torque density, it operates at the level of a PSM.
ZF plans to develop the I2SM technology to production maturity and offer it as an option within its own e-drive platform. Customers from the car and commercial vehicle segments can then choose between a variant with a 400V or with 800V architecture.