Folded materials offer lower weight and higher strength
Process could cut tooling costs when making cars and planes
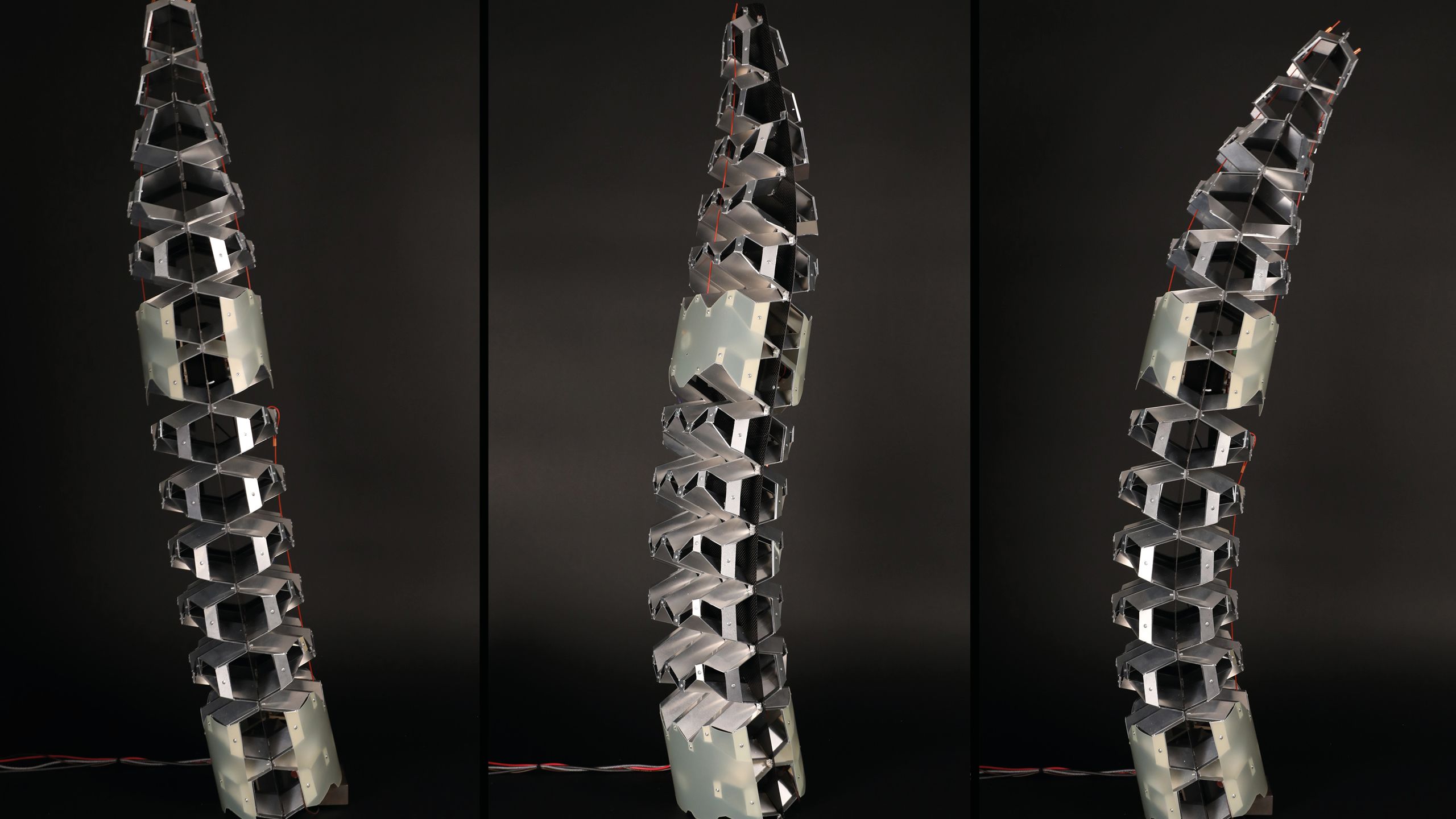
Engineers at the Massachusetts Institute of Technology (MIT) have used kirigami, the art of Japanese paper cutting and folding, to develop ultrastrong, lightweight materials with potential aerospace applications.
The high-performance architected materials, which could be used in aeroplanes, cars or spacecraft, are known as plate lattices and have tuneable mechanical properties, such as stiffness and flexibility.
Built on a much larger scale than in previous projects thanks to additive manufacturing, the structures with custom shapes and tailored properties were made from metal and other materials. They could also find use in construction applications.
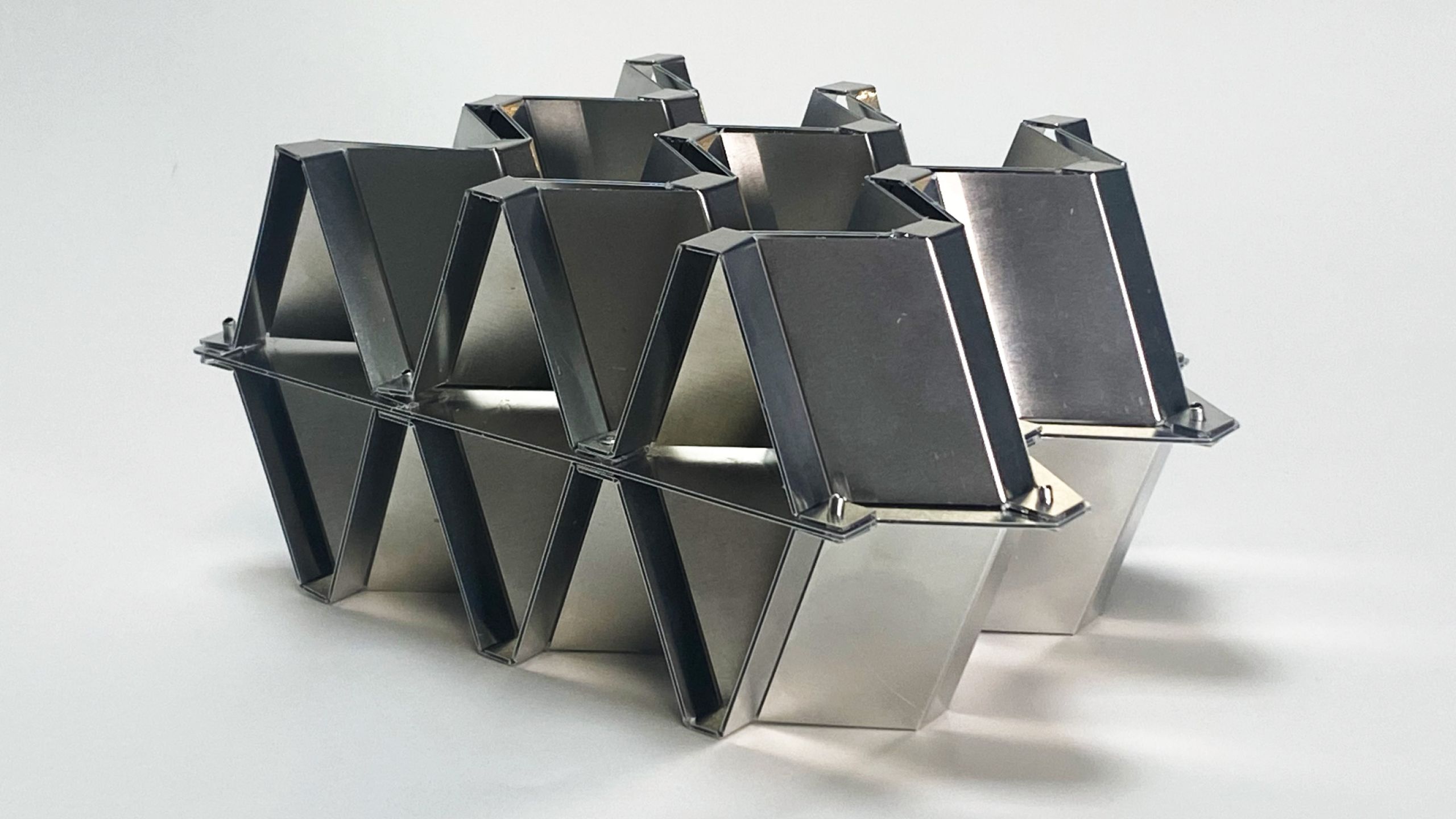
“This material is like steel cork. It is lighter than cork, but with high strength and high stiffness,” said Professor Neil Gershenfeld, senior author of a new paper on the work.
The researchers developed a modular construction process in which many smaller components are formed, folded and assembled into 3D shapes. Using this method, they fabricated ‘ultralight and ultrastrong’ structures and robots that, under a specific load, can morph and hold their shape.
The MIT researchers modified a common origami crease pattern, known as a Miura-ori pattern, so the sharp points of a corrugated structure are transformed into facets. The facets provide flat surfaces to which plates can be attached more easily, with bolts or rivets.
“Plate lattices construction has been so difficult that there has been little research on the macro scale. We think folding is a path to easier utilisation of this type of plate structure made from metals,” said co-lead author Alfonso Parra Rubio.
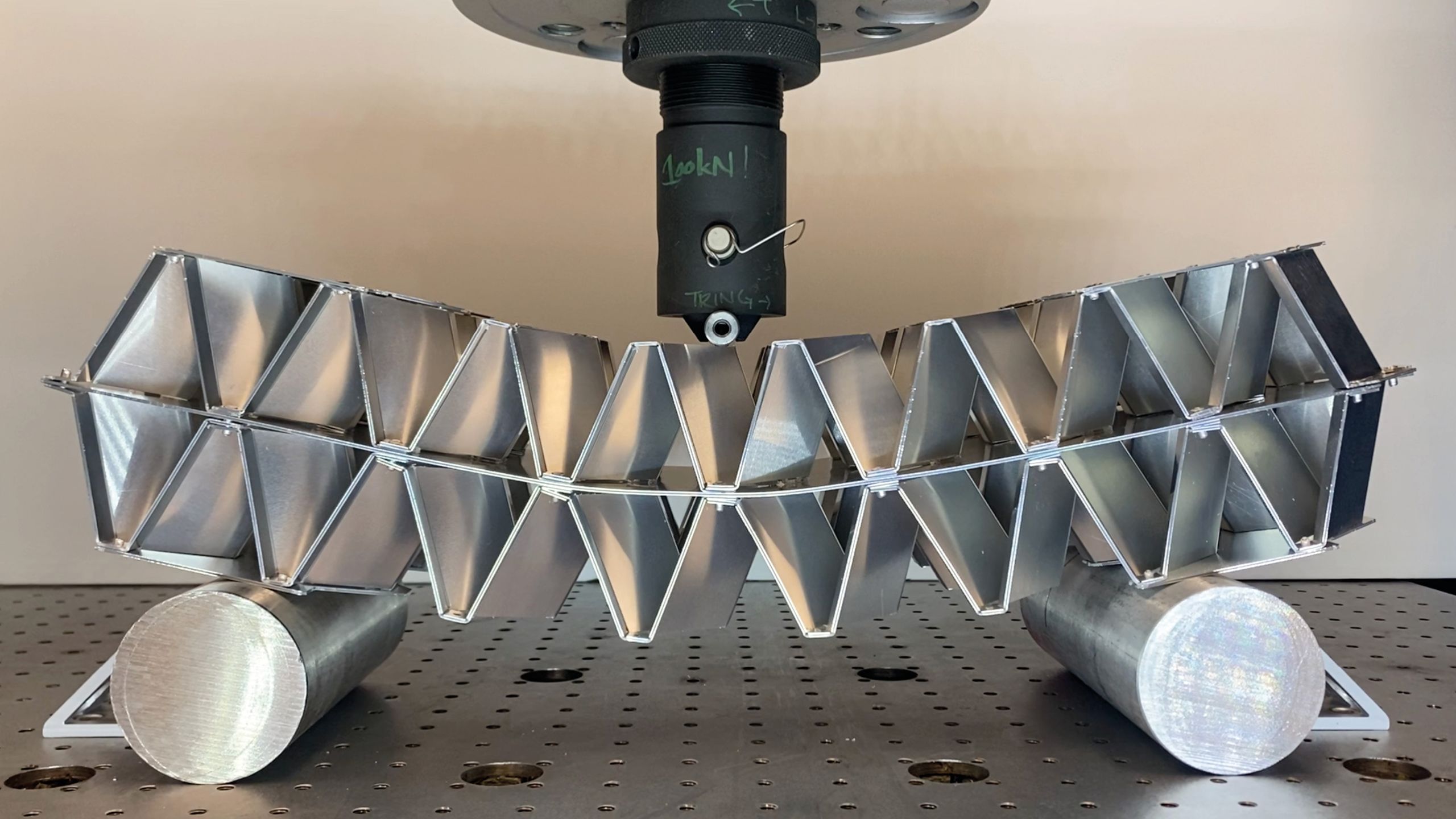
Based on the way the folds are designed, some cells can be shaped so they hold their shape when compressed, while others can be modified so they bend. In this way, the researchers could precisely control how different areas of the structure deformed when compressed.
“Because the flexibility of the structure can be controlled, these corrugations could be used in robots or other dynamic applications with parts that move, twist and bend,” said the MIT announcement.
To craft larger structures such as robots, the team used a modular assembly process, mass-producing smaller crease patterns and assembling them into 3D structures. Smaller structures have fewer creases, which simplifies the manufacturing process.
“To make things like cars and airplanes, a huge investment goes into tooling. This manufacturing process is without tooling, like 3D printing. But, unlike 3D printing, our process can set the limit for record material properties,” said Gershenfeld.
Using their method, the team produced aluminium structures with a compression strength of more than 62kN, with a weight of 90kg per square metre. The structures were reportedly so strong that they could withstand three times as much force as typical corrugated aluminium.
You're reading a brand new digital publication from the team at Professional Engineering. We'd love your feedback: let us know what you think at profeng@thinkpublishing.co.uk