PROCESS
DIGITAL DOLLARS
Digital technologies are delivering a big boost to economies, with process engineering showing the way.
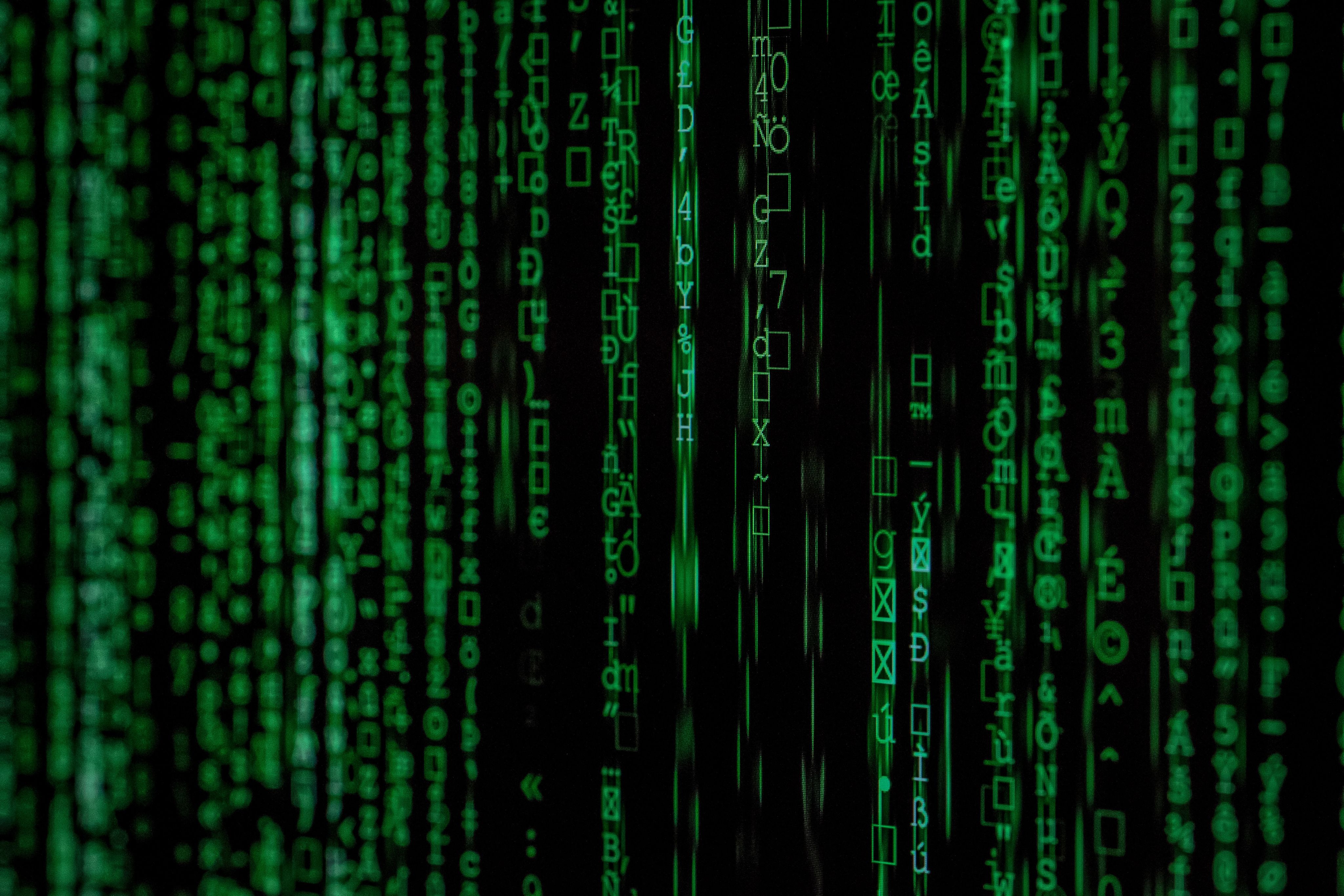
In an era driven by rapid technological advances, the process engineering sector finds itself at the crossroads of change, with digital transformation reshaping its landscape. Digital transformation, the integration of digital technology into all aspects of business operations, is not only altering the way companies function but is also playing a pivotal role in enhancing productivity, reducing costs and ensuring sustainability.
Industry 4.0 is at the heart of digital transformation in the process engineering sector. Advanced technologies such as the Internet of Things, artificial intelligence and big-data analytics are being harnessed to optimise operations and enable predictive maintenance.
Better decisions
According to a report by PwC, embracing Industry 4.0 technologies could add £445bn to the UK economy by 2030, with the manufacturing and process sectors being significant contributors.
One of the most substantial benefits of digital transformation is the ability to capture, analyse and act upon real-time data. In the process engineering sector, this translates to efficient monitoring and control of operations, enabling quicker responses to changing conditions. For instance, in the chemical industry, sensors embedded in production equipment can collect data on temperature, pressure and other variables. This data is then analysed in real-time, allowing engineers to make informed decisions and prevent potential breakdowns.
“Distributed control systems (DCS) have been helping to ensure reliable, efficient and safe performance of industrial processes for over 40 years,” explained Johan Björklund, head of product line management at ABB Process Automation. “During this time, the technology has been refined and adapted to reflect growing requirements.
“With the advent of digitalisation, this refinement is now being taken one step further, with the Digital DCS offering a raft of exciting new opportunities for maximising productivity, collaboration and operator engagement without compromising any of the core functions of the DCS itself.
“With sustainability now a key part of the corporate agenda, the potential offered by digitalisation will also help to ensure that the DCSs of the future can play a major role in helping companies to achieve their net-zero targets.”
Predictive maintenance, powered by AI and machine-learning algorithms, is transforming maintenance practices in the sector. Rather than adhering to traditional, calendar-based maintenance schedules, companies are now able to predict when equipment might fail based on data patterns. This approach minimises downtime and reduces maintenance costs.
Digital transformation is not only improving operational efficiency but also enhancing safety in the process engineering sector. AI-driven simulations are being employed to model and predict potential hazards, enabling engineers to take preventive measures, reducing the risk of accidents.
Cutting carbon
Moreover, digital solutions are aiding companies in their sustainability efforts. Energy consumption can be optimised using data analytics, leading to reduced carbon footprints.
“Historically reluctant to invest in technology, oil and gas companies are now embracing cloud and IoT to improve operational efficiency, visibility and safety,” said Martin Phillips, product manager at Fluenta. “The explosion of IoT technology will drive developments in connected products, software and techniques – providing new opportunities for accurate reporting, improved risk management and regular maintenance.”
While digital transformation offers numerous benefits, it also presents challenges that the sector must navigate. Integration of legacy systems, cyber-security concerns and the need for upskilling the workforce are among the key hurdles.
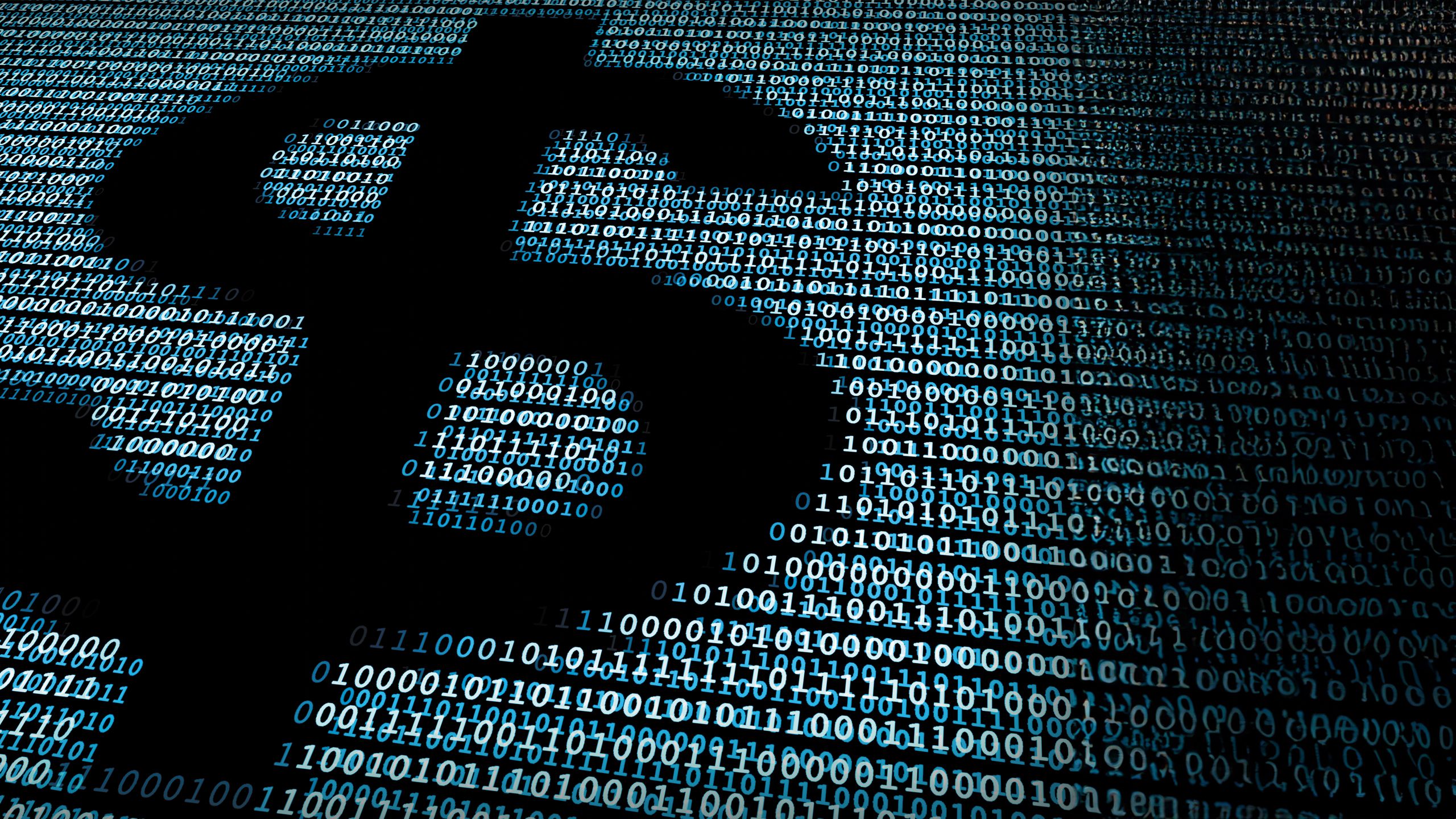