Winging it for sustainability
Longer, thinner and ‘morphing’ wings could cut aviation emissions by boosting aerodynamic efficiency. Aerospace giants including NASA and Airbus are hard at work – but radical change is not going to be easy
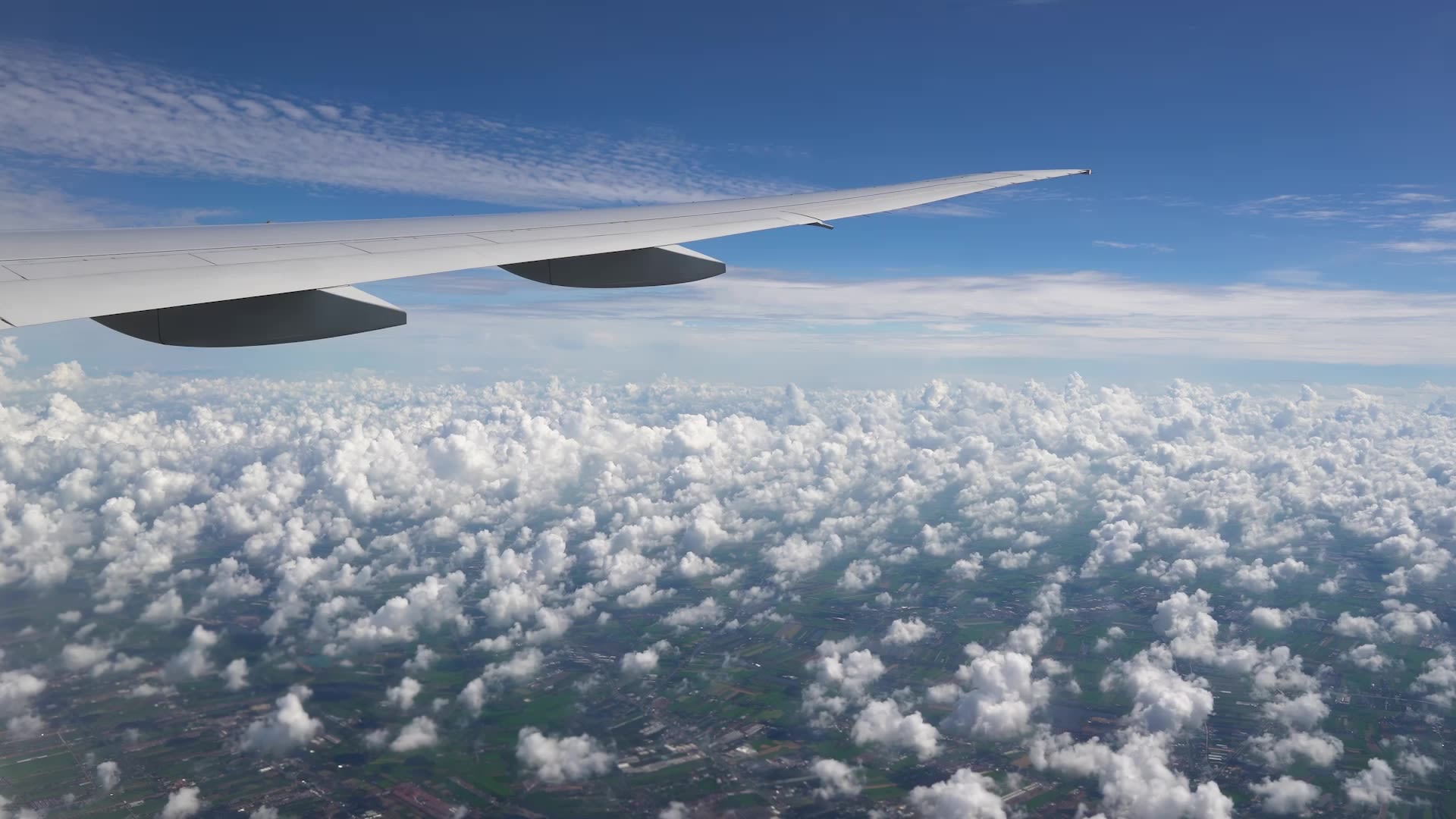
The race for sustainable flight is on. Companies, governments and research organisations around the world are exploring everything – from hydrogen fuel cells and sustainable aviation fuel (SAF) to aerodynamic coatings – in the search for a way to cut emissions.
Many of these bold ideas are at a very early stage, especially when compared to the giant, globe-spanning scale of the aviation industry. Brand-new technologies are needed, and manufacturing and processing capabilities need rapid upgrades if we are ever going to see a genuine shift to carbon-neutral or zero-carbon fuels.
It might seem unlikely, therefore, that we could achieve deep and meaningful reductions in fuel use by altering something as fundamental and well-understood as the aeroplane wing. But that is exactly what NASA, Boeing, Airbus and others are trying to achieve. By changing their shape and enabling new ‘morphing’ capabilities, researchers hope that wings could provide a major lift for sustainability efforts.
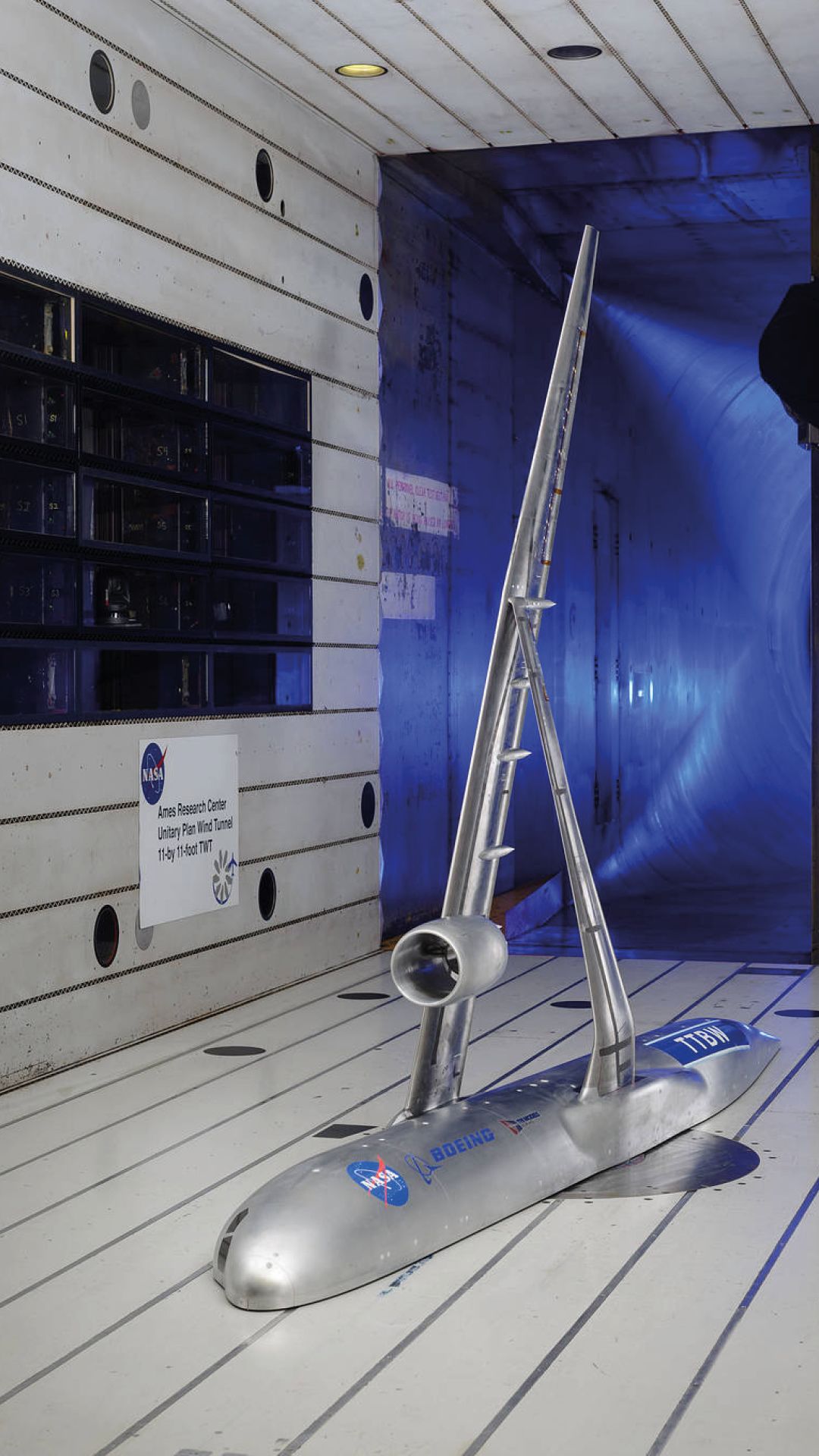
A certain ratio
In Palmdale, on the edge of the Californian desert, a Boeing MD-90 is undergoing a radical transformation. The wings of the former single-aisle airliner will be replaced with longer, thinner wings supported by aerodynamic trusses as it becomes the X-66A, NASA’s newest experimental plane.
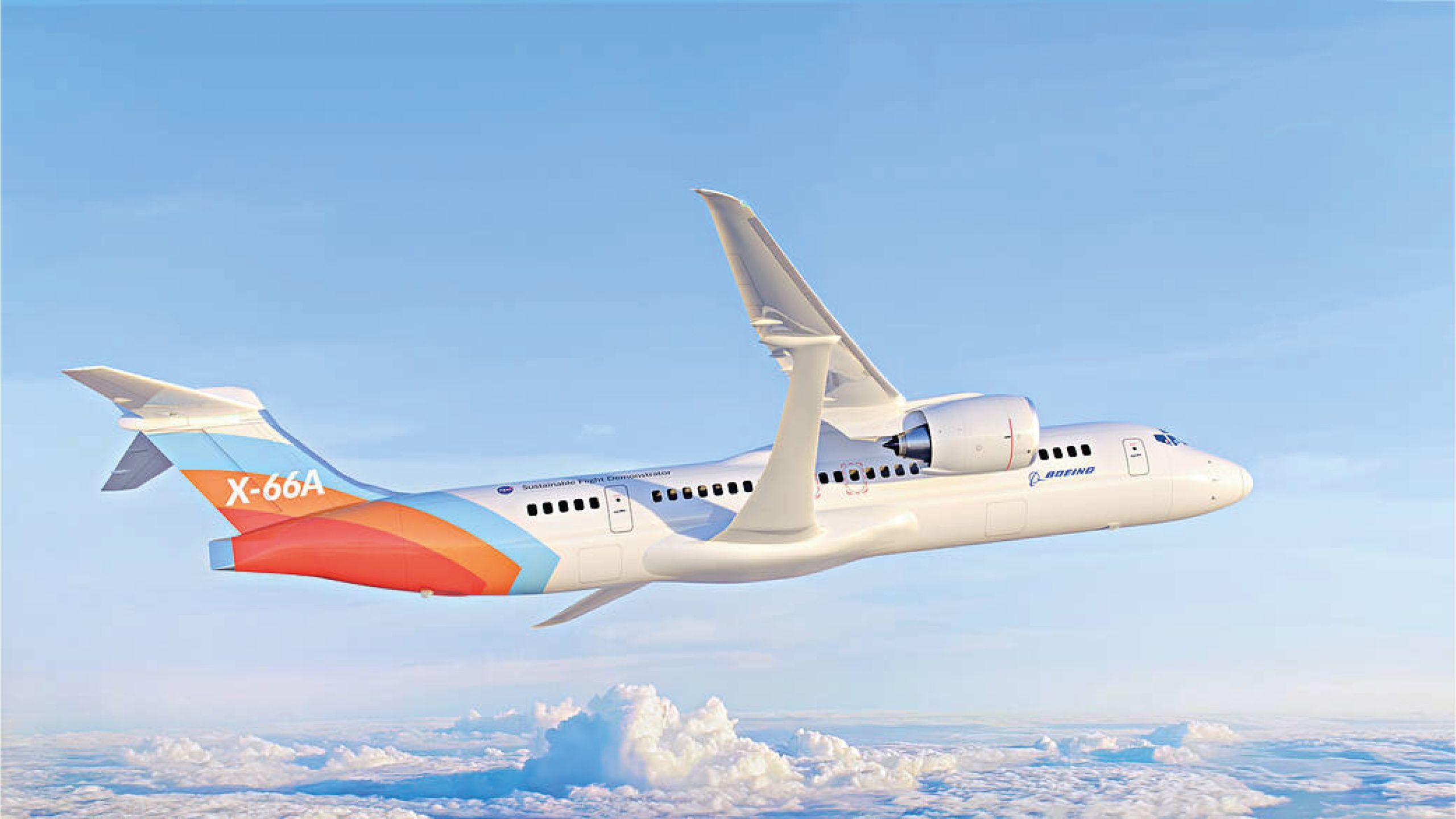
The Transonic Truss-Braced Wing (TTBW), as the design is known, could produce less drag and therefore cut fuel use by 5-10%, NASA claims. Combined with other technological advances – such as new propulsion systems, which the agency said could be more easily accommodated on larger wings – that could increase to 30%.
The project is one of several schemes to cut emissions by boosting the aspect ratio of an aircraft’s wings, making them longer and more slender to increase lift and reduce drag.
“It’s why birds that fly over long ranges, like albatross, have long slender wings, because then they can just soar on the air currents,” says Sue Partridge at Airbus.
The head of the company’s Filton site in Gloucestershire, which designs the wings that ‘half of the world’s air passengers fly on,’ is also in charge of the Wing of Tomorrow programme. The project is focused on design and manufacturing techniques for “longer, leaner, lighter, high-performing wings,” says Partridge.
The aerospace giant hopes that the aerodynamics of the wing could make as big a contribution to fuel efficiency as the next generation of engines, but achieving that will be far from easy.
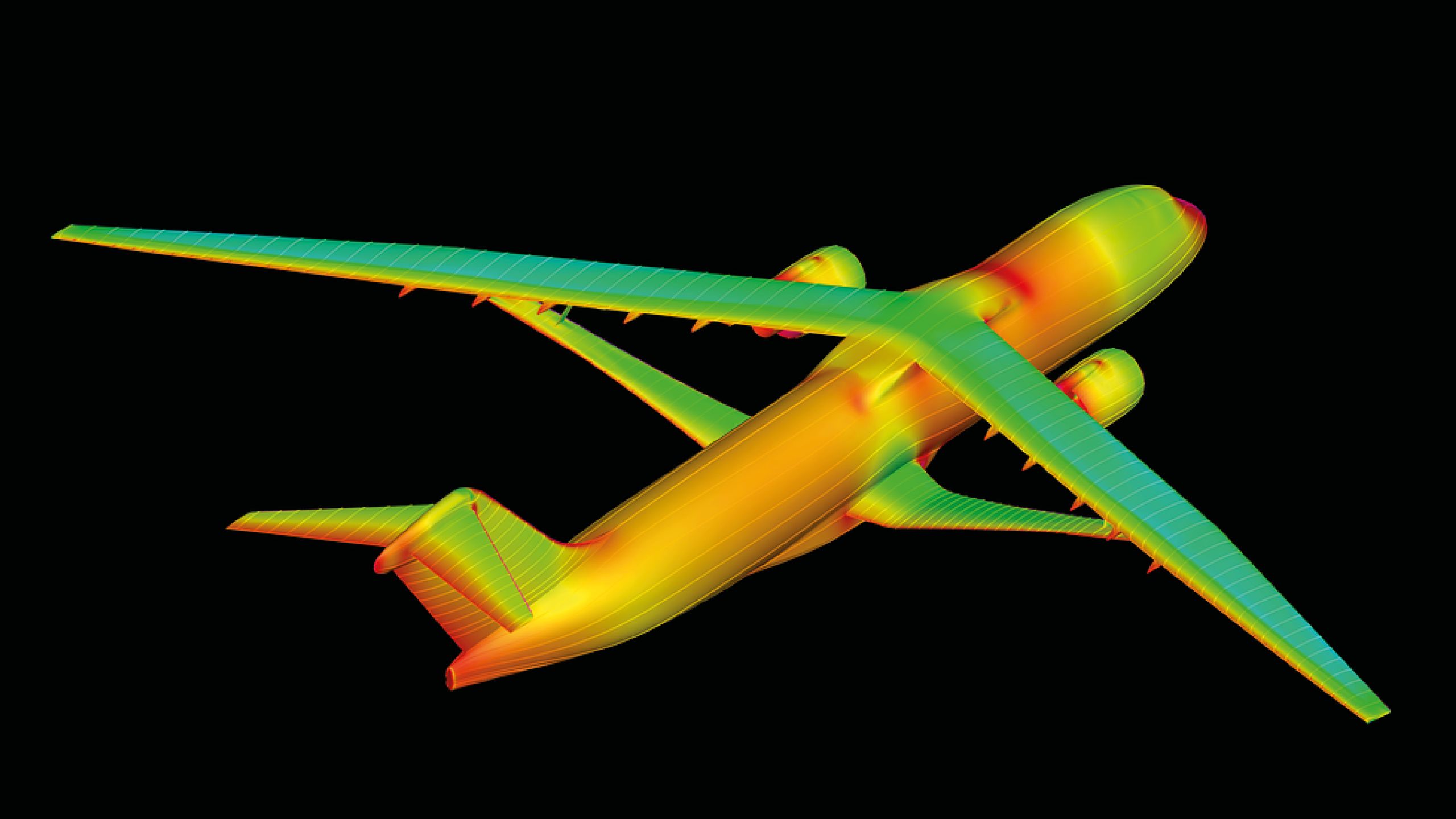
“My job running a technology programme is to investigate multiple options so that we can make trades,” says Partridge. “If you make the wing longer then it's going to be more expensive – and it's going to be heavier actually, because it's longer. So then you'll be trading that against how much fuel efficiency that gives you.”
Improving wing design has one huge advantage, however – it can boost efficiency regardless of the engine and fuel type being used.
"We took inspiration from birds. It changes the shape of the wing in each part of flight to be efficient. If it’s loitering and gliding it’s one shape, if it lands it’s another shape – so the goal is to have these kinds of shape changes."
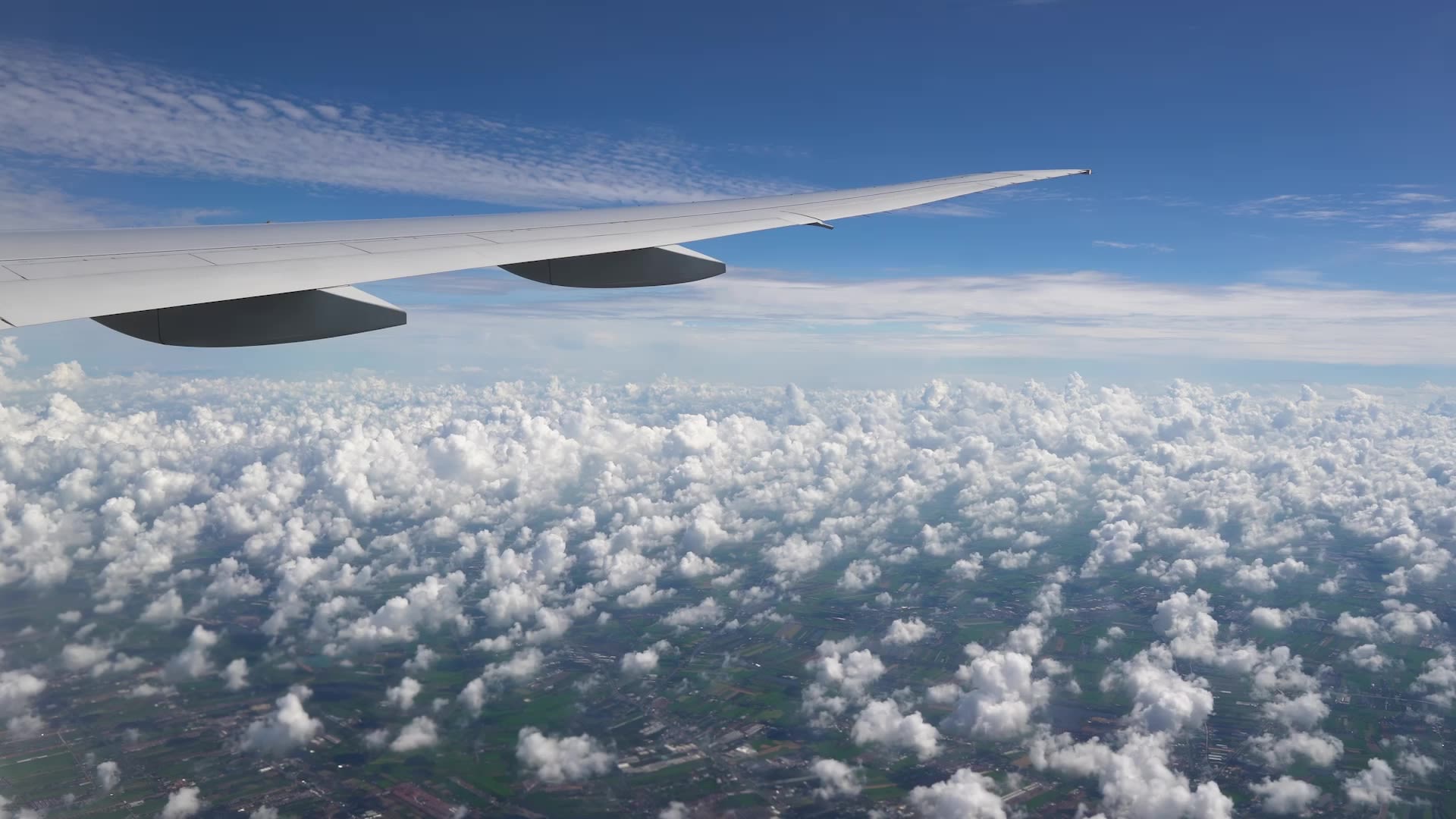
Taking a load off
The albatross also inspired a 2019 Airbus project that is influencing ongoing work. The AlbatrossONE was a small remote-controlled aircraft demonstrator with semi-aeroelastic hinged wing tips, meaning they could flex and react to gusts of wind.
“You can reduce the amount of load on the wing by having the ability to move and alleviate load in certain circumstances,” says Partridge. “If you can reduce the load on the wing, that gives you the chance to have a really nice long span and reduce the weight.”
The Wing of Tomorrow programme is also exploring technologies that might move other parts of the wing to achieve a similar effect, she says, such as the surfaces along the back edge – although the increased complexity, costs and weight that might be incurred make it another trade-off.
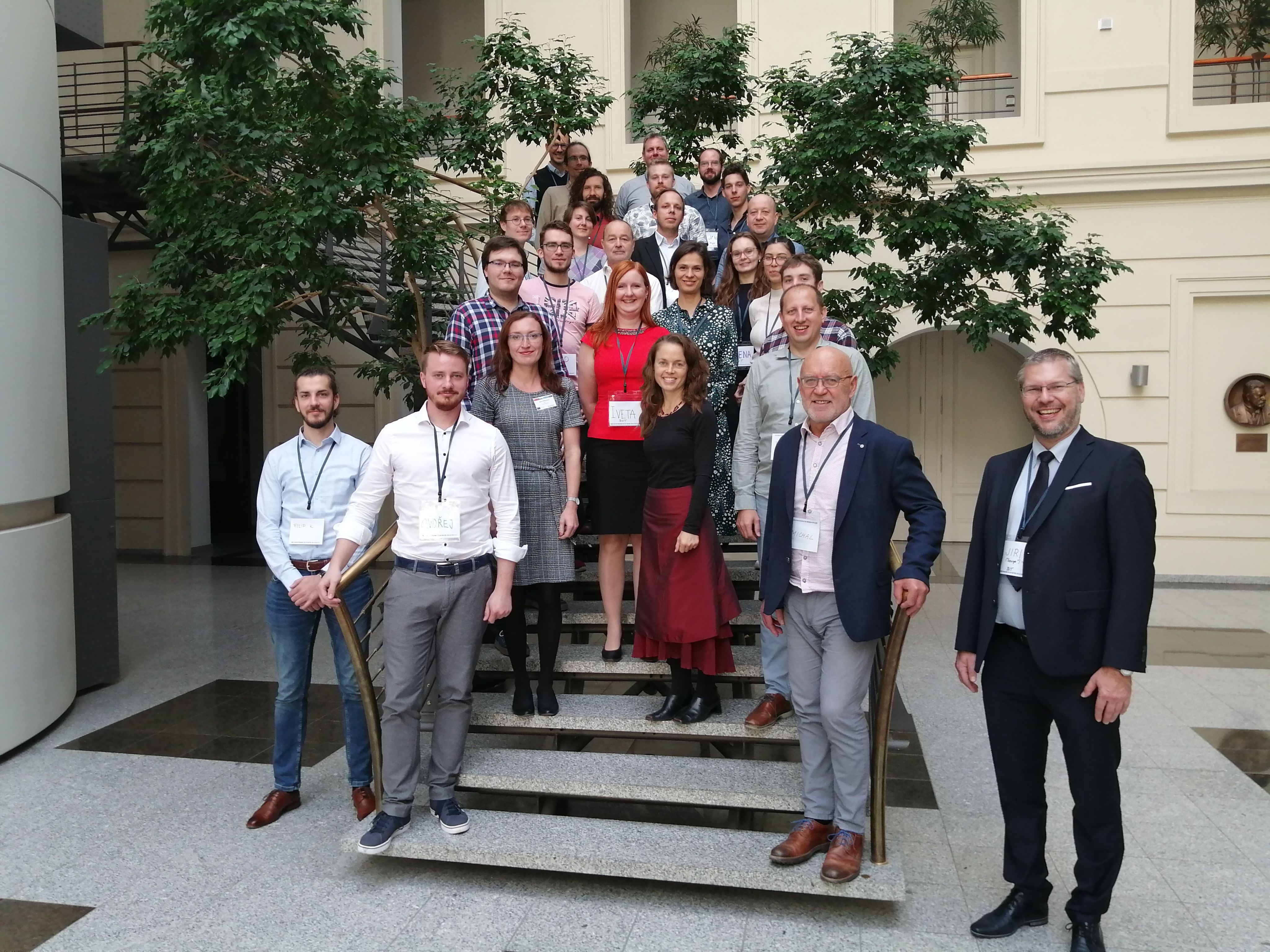
Mighty morphing
Changing the shape of the wings in flight is also being explored in the Baang (Building Actions in Smart Aviation with Environmental Gains) project, an EU-funded collaboration between Imperial College London, Brno University of Technology in the Czech Republic, TU Delft in the Netherlands, and TU Wien in Austria.
As with projects at Airbus, nature’s most nimble flyers were an obvious influence for the work. “We took inspiration from birds,” says Jan Navratil, assistant professor at Brno. “It changes the shape of the wing in each part of flight to be efficient. If it’s just loitering and gliding it’s one shape, if it lands it’s another shape – so the ultimate goal is to have these kinds of shape changes.”
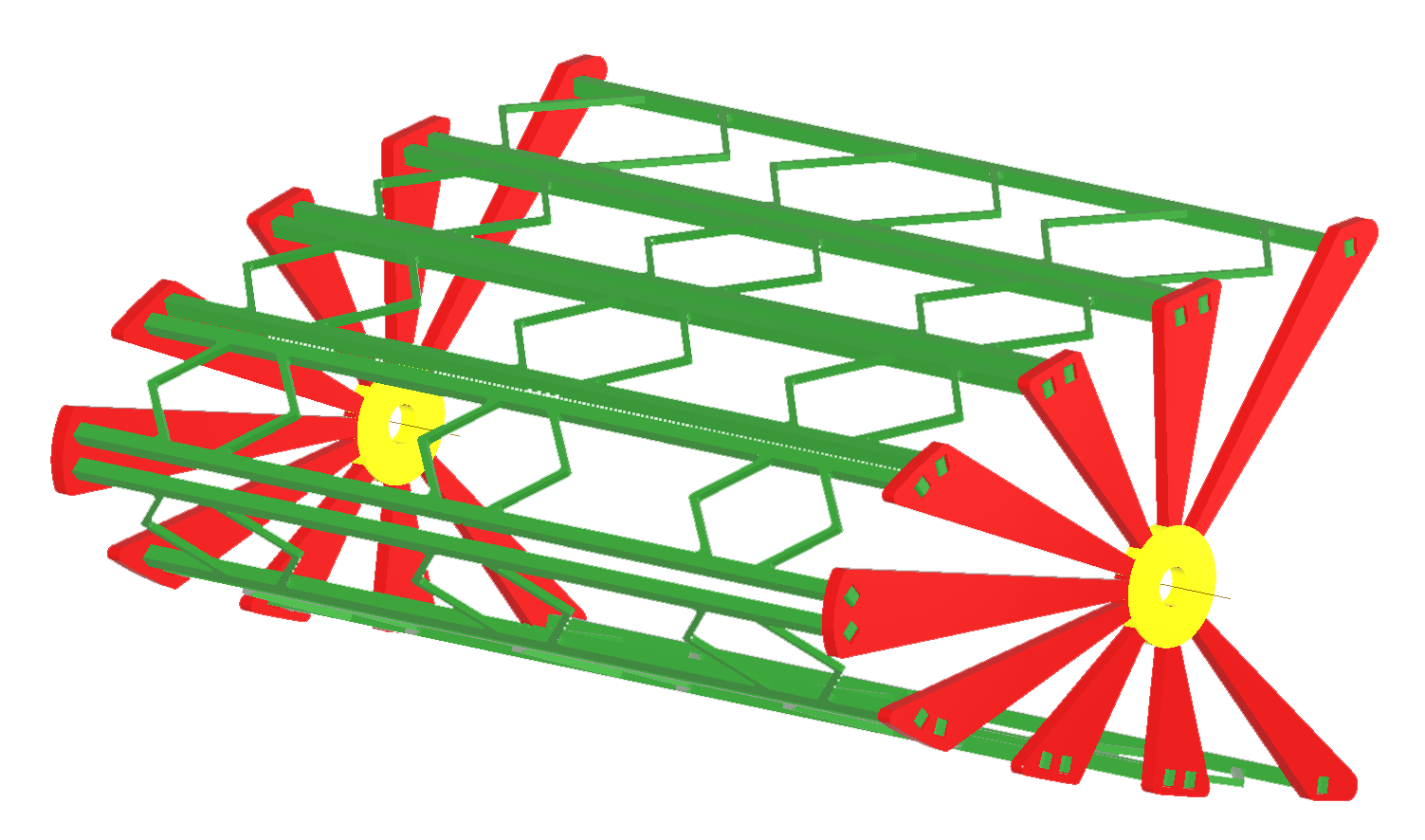
This ‘morphing’, which researchers hope could provide the optimal aerodynamic profile for each stage of flight, will change the shape of the wing’s trailing edge or winglet. The team aims to use metamaterials – which have properties that are otherwise impossible in nature – to switch between predetermined shapes, although they are not designed to replace primary aircraft controls such as the elevator, aileron and rudder.
As well as lowering drag and structural weight – and therefore fuel consumption – the researchers hope morphing wings could improve passenger comfort. From the outside, they might look like a homogeneous surface, with actuators that move and change the shape hidden beneath the surface.
The structure will need to morph without an increase in mass, says Navratil. Other challenges include finding a surface that offers better aerodynamic properties than current commercial options, and deciding on the internal actuator configuration that can provide continually adapting shapes.
Manufacturing such a complex new system will be another challenge, says Navratil, with metal additive manufacturing being explored as an option.
“The goal of the project is to provide some technology which will help in this effort to reduce fuel consumption and greenhouse-gas emissions,” he says. “If this structure, due to 3D printing, can provide some and structures which are lightweight… you can either increase the payload, in the future the number of passengers, or we can also decrease the fuel consumption again.”
The team aims to have a ground-based demonstrator by the end of the project in two years, followed by testing on a drone, which could influence airliner design in future.
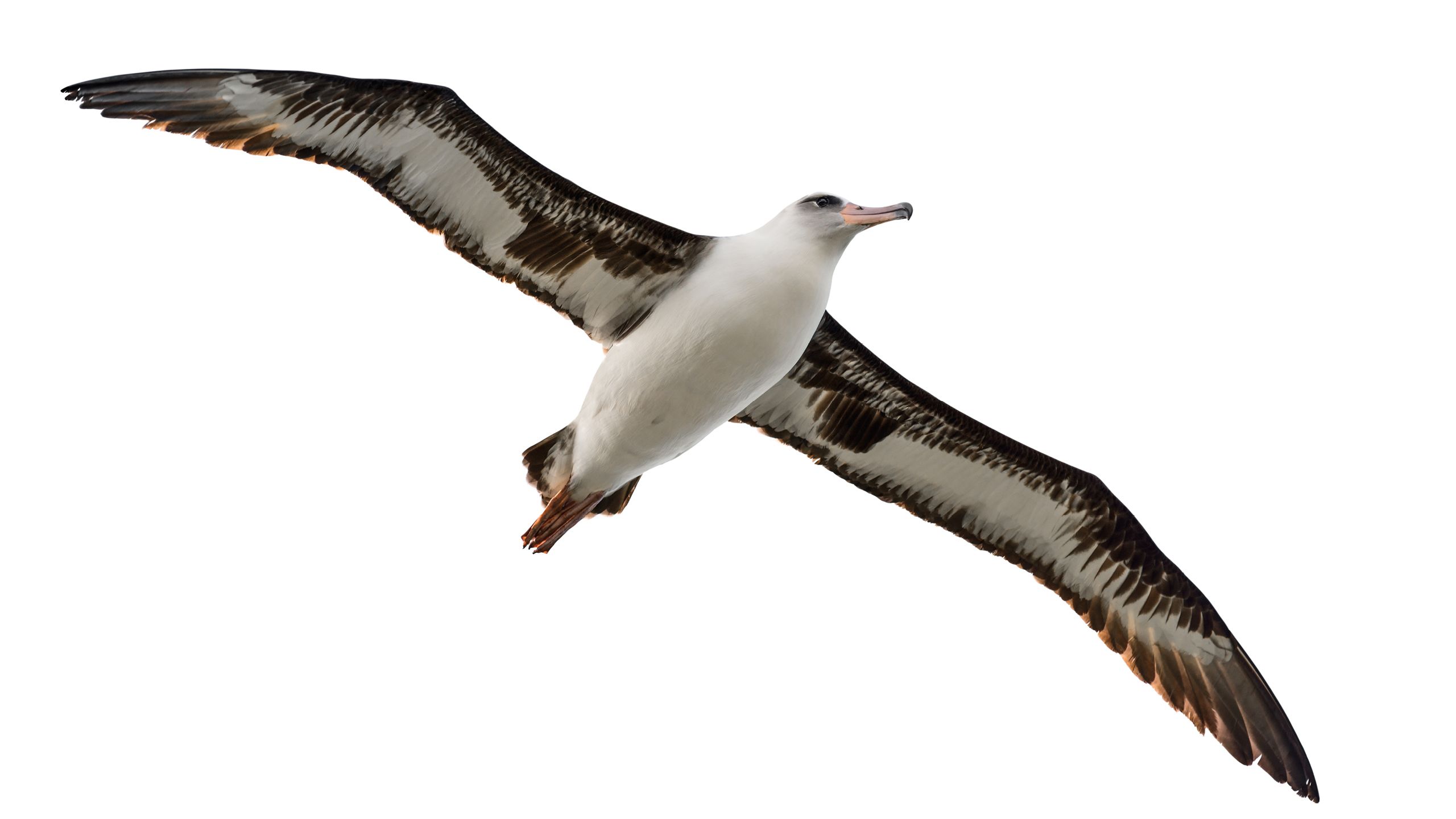
Blending in
The future might bring even more extreme changes to wing structure. Airbus is still exploring ‘blended wing’ designs, for example, in which the wings and fuselage are blended together into one smooth structure.
“You're then trying to trade between passenger space as well as performance, as well as weight, as well as cost,” says Partridge. “It's like having a menu of options that you're going to choose from, and you need to look at all of the pros and cons of all of those different options.”
It might be tempting to think of simpler wing upgrades as low-hanging fruit compared to new engines or fuels, but the nature of the aerospace industry brings some significant challenges. Manufacturing is a major hurdle, and is receiving a lot of attention at Filton.
Dr Estela Bragado, a research fellow in flight modelling and simulation at Cranfield University in Bedfordshire, is involved in an Airbus project developing methods for rapid prototyping. Simulation will play a key role in getting new designs off the ground, she says, enabling a “holistic” approach that can assess the introduction of multiple new technologies at once.
Wing projects need to go hand-in-hand with work on fuels and propulsion to have the biggest impact. “Everything has to go together,” says Bragado. “For us to be able to go further in wing design, we also need to develop the technologies that go around it.”
She adds: “You want to try different propulsion technologies in different wing configurations. What if we expand it to a family of aircraft, so what if we have one for regional flight routes, another one for transonics and so on. We want to be able to increase our control in the decision making and have more interactivity, so we'll be able to visualise the dependencies between our design criteria.”
Radical upgrades
Given the amount of work to do, it might be some time before we see commercial flights with longer, trussed, morphing or otherwise significantly different wings. Certification and safety standards will be another hurdle to clear.
“It is difficult to achieve that level of safety, that standard that we want and we need,” says Bragado. “The more we go away from our traditional designs, the more difficult it is going to be to certify them and show that they are safe.” Simulation could accelerate this process, however, and she expects a “revolution” in certification in the coming years.
Looking further ahead, radical designs such as the blended wing might solve some problems but bring new issues that also need consideration, she adds – but there is still reason to be hopeful about the future of aviation.
“We are in a stage in which there is this push from everyone – from society, from the environment, from us,” she says. “We are addressing this challenge, we are going for it and we're taking the time to research and to act towards it. So I think it's good, it's fast moving – fast within the scale of aviation.”
You're reading a brand new digital publication from the team at Professional Engineering. We'd love your feedback: let us know what you think at profeng@thinkpublishing.co.uk