BLAST OFF
These four trends and technologies showcased at Farnborough International Airshow (20-24 July) could transform the future of energy, transport, manufacturing and the space industry.
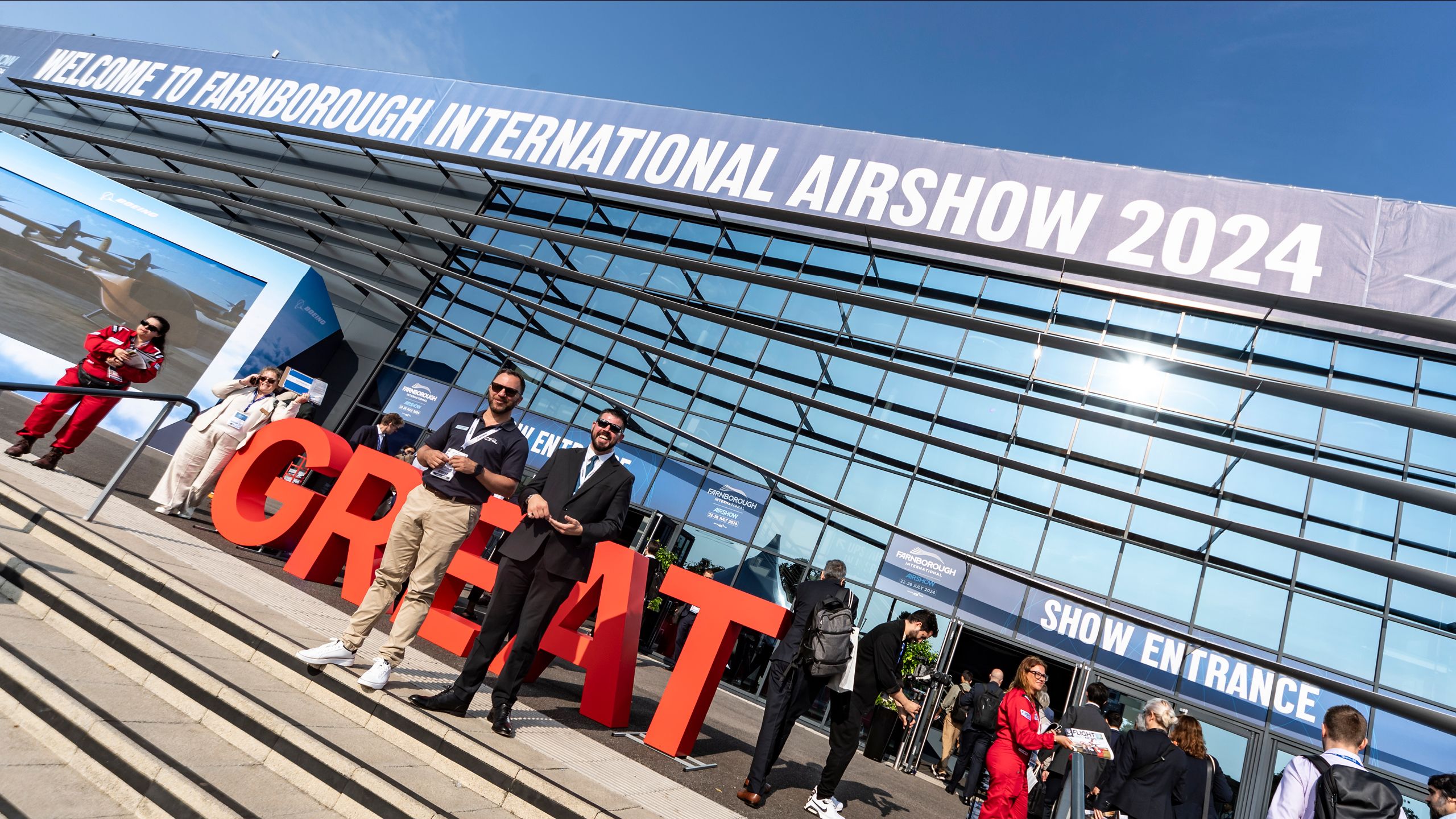
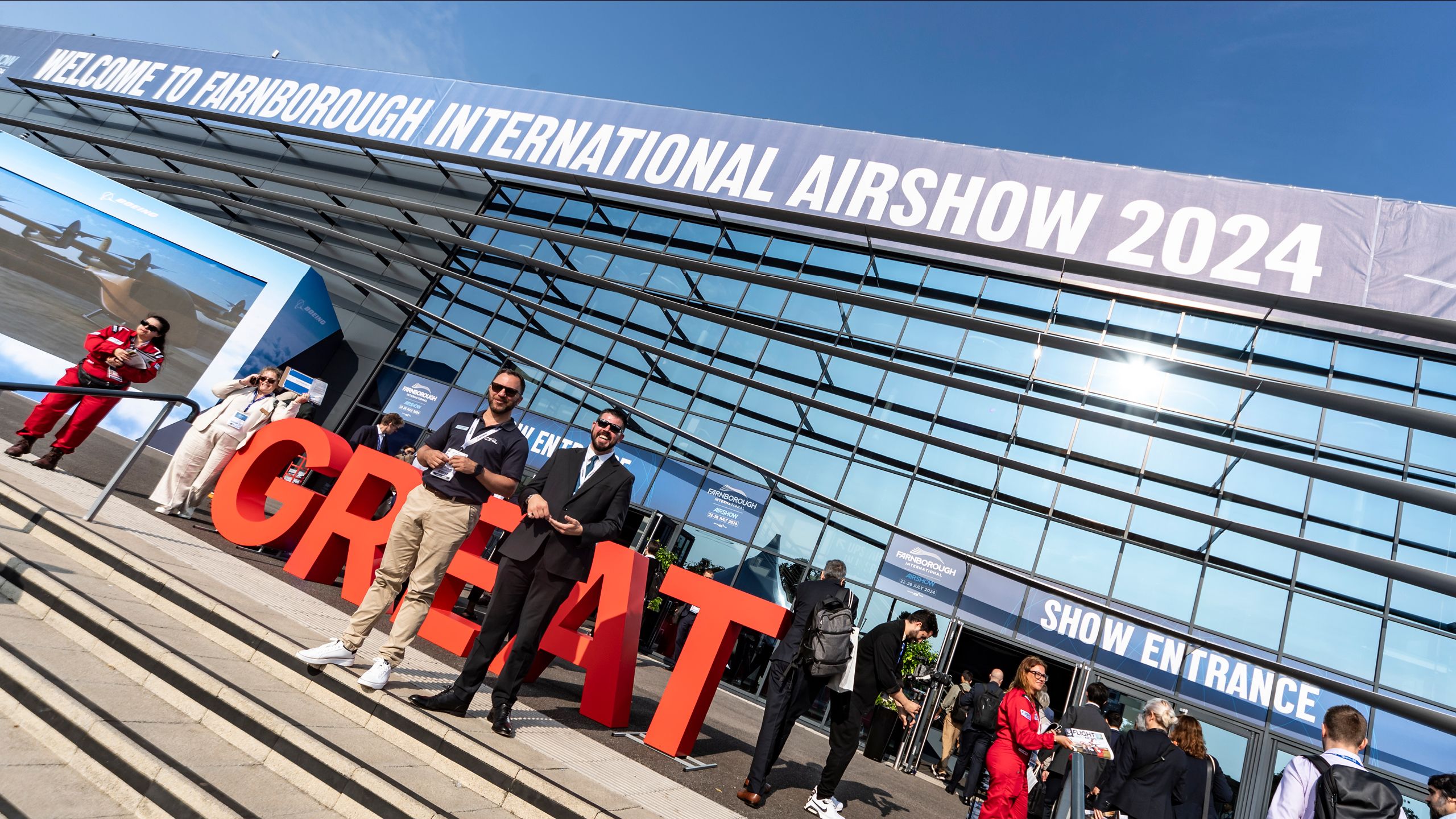
1. World’s biggest plane could boost onshore wind
Transporting wind-turbine blades by road is no easy task. Stretching for 50m or more, they make driving round even the slightest of bends in a narrow rural road a complex logistical challenge.
This means that current deployments are in “the most cherry-picked locations,” said Paul Hanna, marketing executive at energy company Radia. “You can't turn corners. You can't get them under bridges – and for those that you can, it literally takes a year-and-a-half to plan to move, by ground, one blade from the manufacturing facility or the port of entry to the windfarm.”
Transporting turbine blades by road is a giant logistical challenge
Transporting turbine blades by road is a giant logistical challenge
Blades on future turbines will be even longer – maybe even 100m or more, which Radia claims is much too long to travel by road. But what if disruption could be avoided by transporting blades by aircraft, landing close to the installation site?
The Colorado firm aims to provide that with WindRunner, which will be the world’s largest aircraft if the project is successful. Aerospace multinational Leonardo will develop the fuselage, Radia announced at Farnborough, while Spanish company Aernnova will partner on development of the aircraft’s wing and engine pylons, and New York consultancy AFuzion will provide safety and certification consulting.
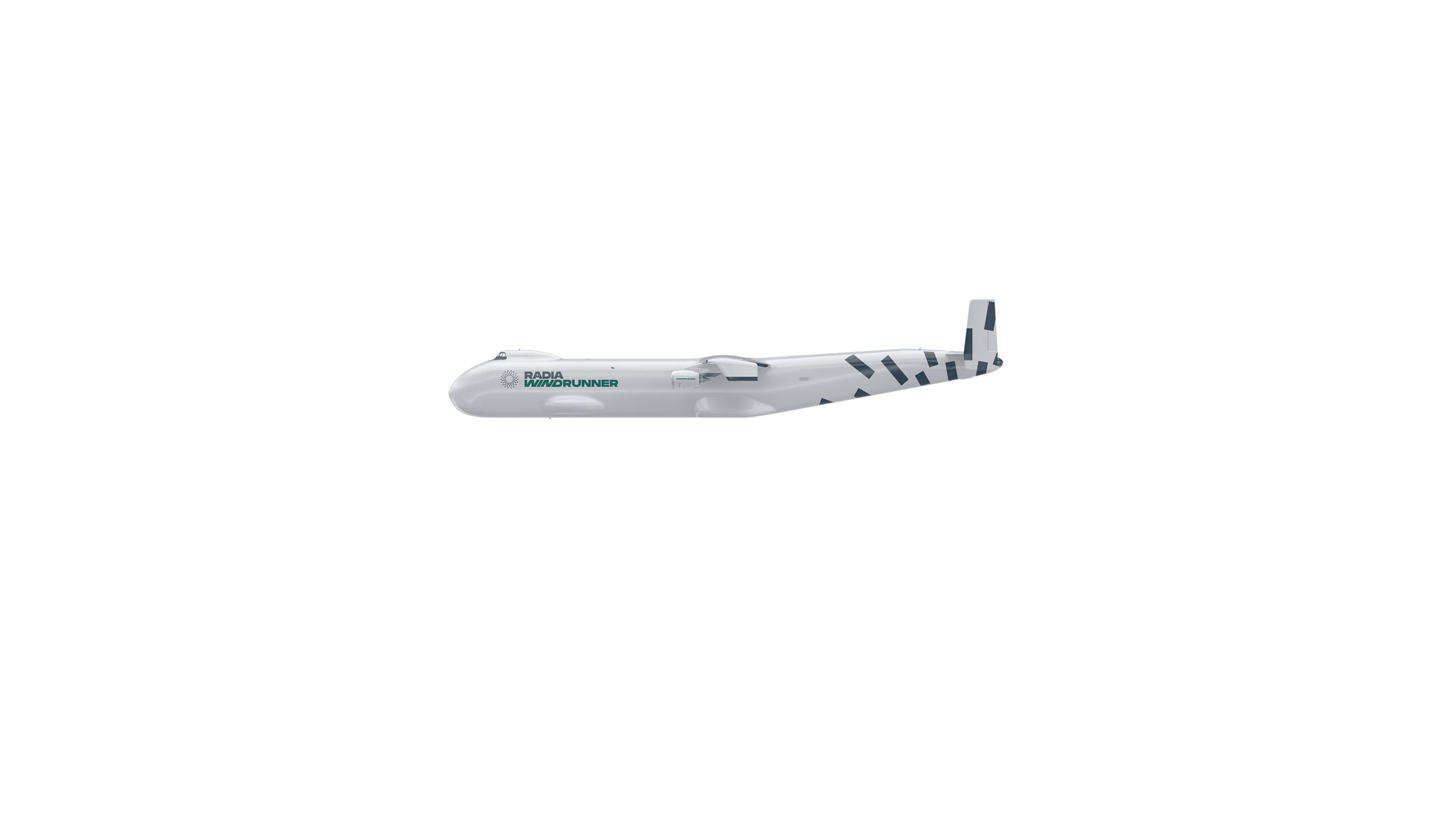
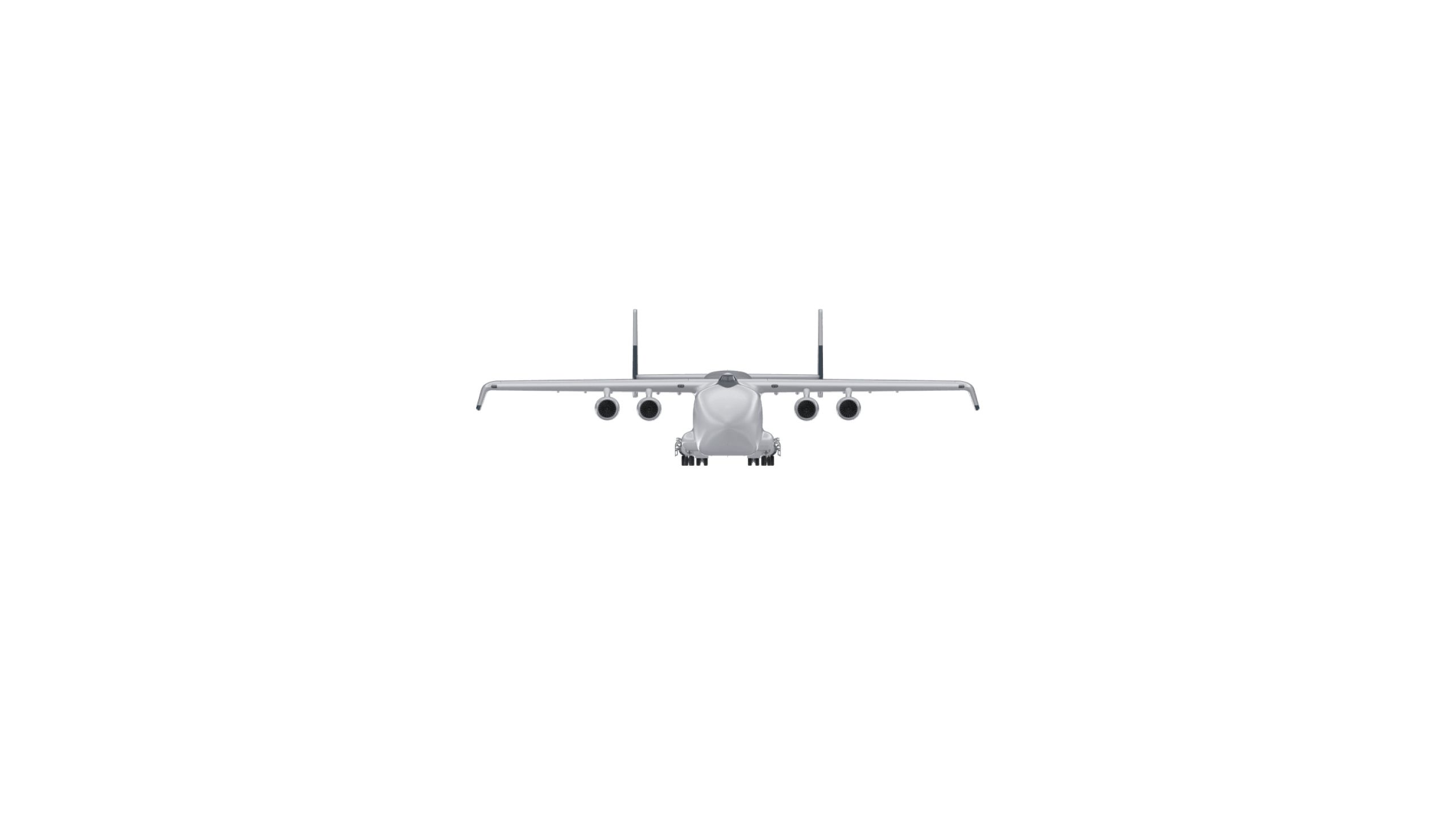
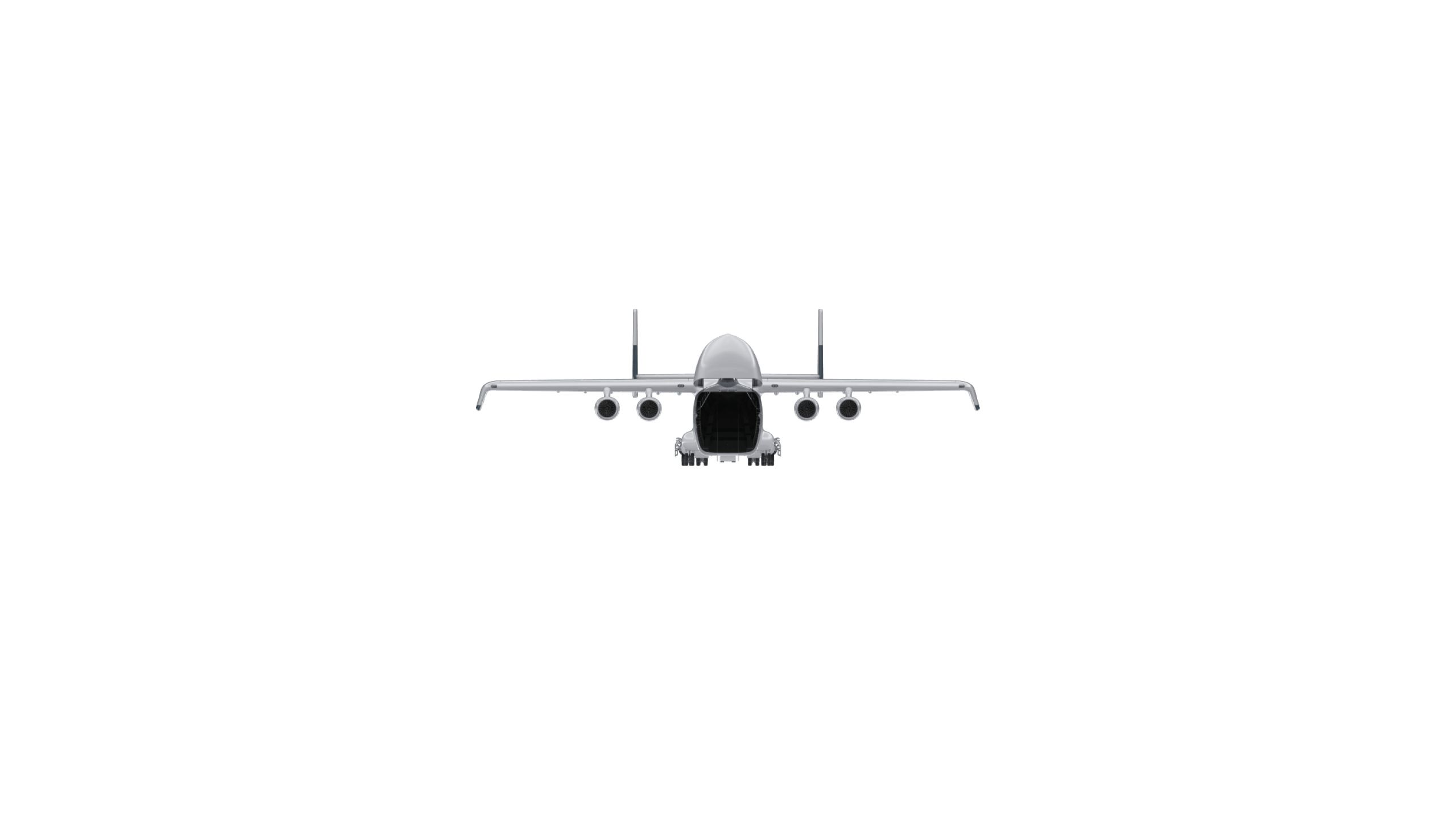
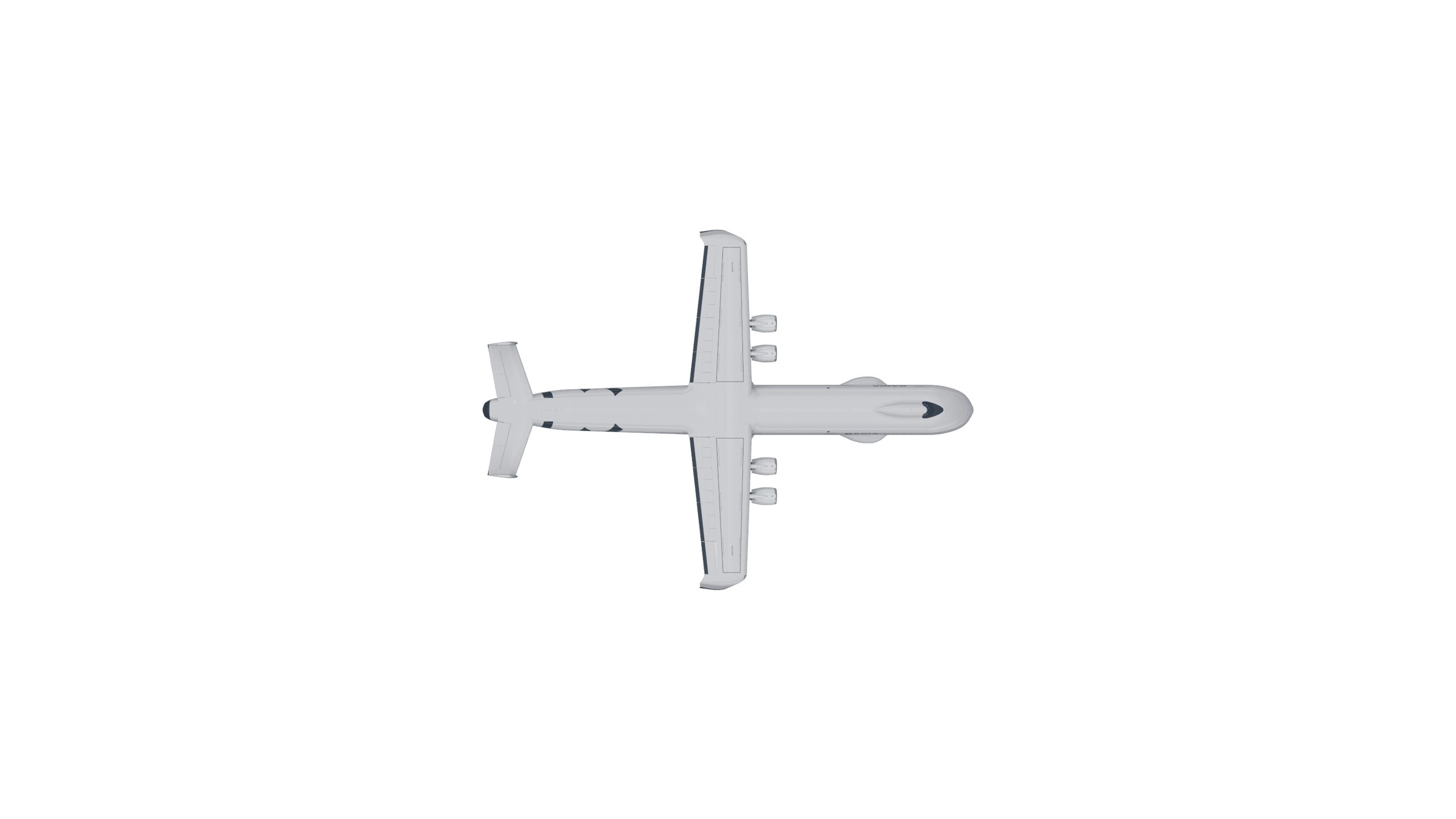
The aircraft is designed to fly turbine blades as long as a football pitch directly to windfarm sites, landing on ‘semi-prepared’ dirt runways as short as 1,800m.
“The innovation that we're bringing to this aircraft is how we're bringing together the existing product catalogue of things that have already been certified and are flying on Airbus and Boeing planes today,” Hanna said. “In some respects, there's no new technology.”
WindRunner could become the world's largest aircraft
WindRunner could become the world's largest aircraft
Illustrations of the aircraft nonetheless reveal a distinctive airframe, including a tall – and extremely long – unpressurised fuselage. Radia is using the philosophy of ‘minimal viable aircraft design,’ Hanna said.
He was unable to provide a specific number of planes they aim to build, but it will be in the dozens. The company aims to triple the acreage available for onshore wind deployment, driving down the cost by 30% in the process.
The aircraft is designed to fly turbine blades as long as a football pitch directly to windfarm sites, landing on ‘semi-prepared’ dirt runways as short as 1,800m.
“The innovation that we're bringing to this aircraft is how we're bringing together the existing product catalogue of things that have already been certified and are flying on Airbus and Boeing planes today,” Hanna said. “In some respects, there's no new technology.”
Illustrations of the aircraft nonetheless reveal a distinctive airframe, including a tall – and extremely long – unpressurised fuselage. Radia is using the philosophy of ‘minimal viable aircraft design,’ Hanna said.
He was unable to provide a specific number of planes they aim to build, but it will be in the dozens. The company aims to triple the acreage available for onshore wind deployment, driving down the cost by 30% in the process.
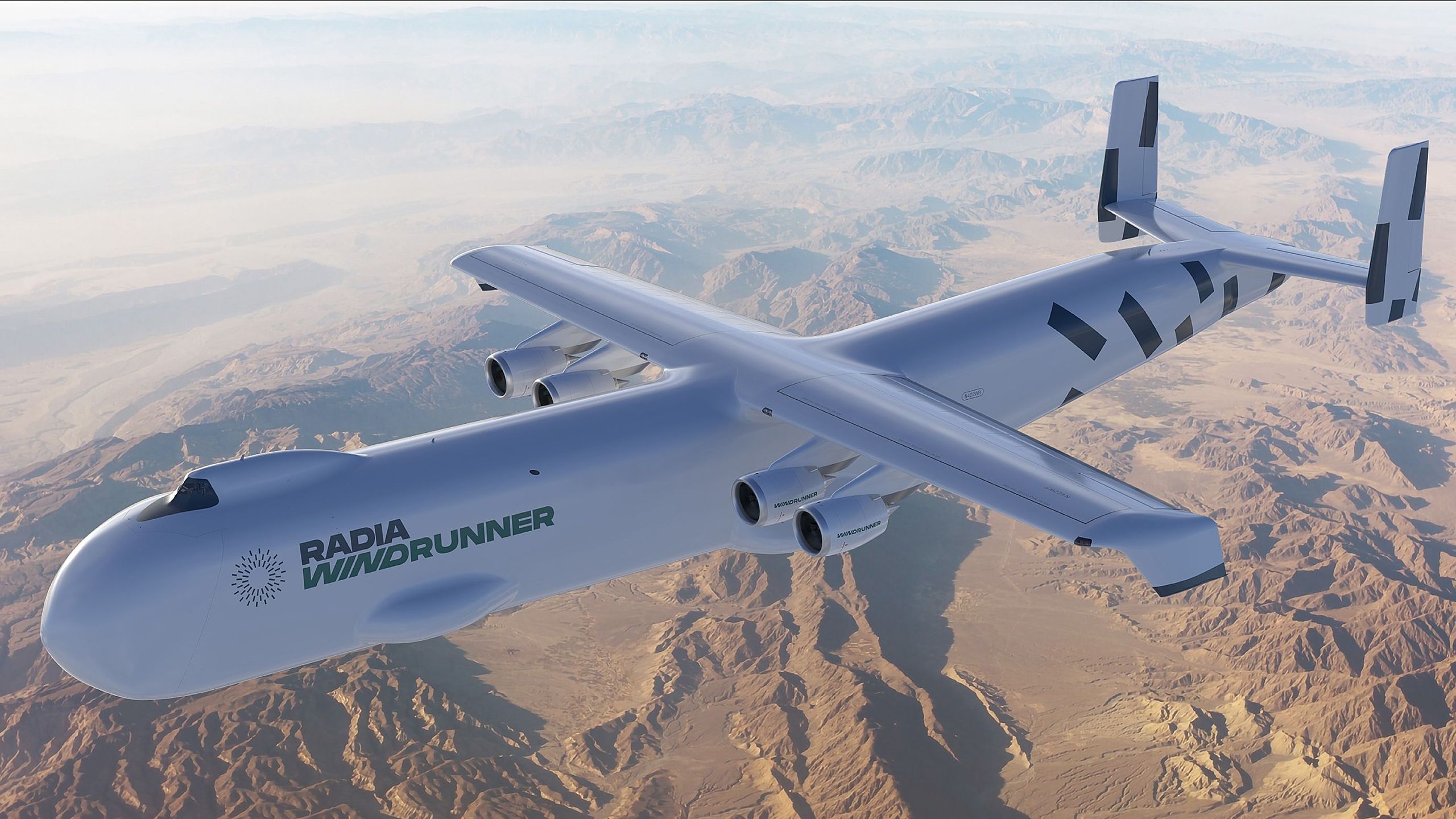
2. ‘Point-to-point’ flights between spaceports
Global same-day delivery could be possible within a few years, according to spaceport operators and spaceplane developers who set out their visions for ‘point-to-point’ deliveries in the airshow’s Space Zone Theatre.
Aiming to take advantage of new technology and expanding spaceport infrastructure worldwide, the panel – led by Global Spaceport Alliance (GSA) chairman Dr George Nield – said high-speed, long-distance transport will carry cargo through the upper atmosphere, before ultimately shuttling people as well.
“I strongly believe that the ability to fly from one point on Earth to the opposite side of the planet in just an hour or two is going to be a tremendous gamechanger, in terms of both national security and economic competitiveness,” said Dr Nield, whose organisation includes 31 worldwide spaceports.
SpaceX’s reusable Starship spacecraft could be well-suited for point-to-point missions, he said, reaching most destinations within 30 minutes and anywhere on Earth within an hour. It could carry up to 150 tonnes of cargo, or several hundred passengers.
Other options could include vehicles from New Frontier Aerospace and Dawn Aerospace, which were both represented on the panel.
The Dawn Mk-II Aurora (Credit: Dawn Aerospace)
The Dawn Mk-II Aurora (Credit: Dawn Aerospace)
US start-up New Frontier’s approach is a vertical take-off and landing (VTOL) craft known as the International Rocketliner, designed to take off from both airports and heliports. The craft will fly at Mach 10+ using renewable LNG in its 3D-printed rocket engine, said chairman Alex Tai. “We can guarantee same-day delivery – and actually in Australia, we can guarantee previous-day delivery (due to proximity to the International Date Line).”
As well as associated emissions, noise pollution is likely to be a key factor in approval or otherwise. Both New Frontier and Dawn have an advantage thanks to their use of rockets, Tai claimed, as air-breathing propulsion systems need to “drag through the lower portions of the atmosphere”.
New Frontier’s craft will travel at 160,000ft (49km), he said. “If we go across the top of London, it will be less than 56 decibels – that's less than a fridge on in the kitchen next door. You won't hear it… on the way down, we reduce from supersonic speeds more than 200 miles away from the destination, so there's no sonic boom over land.”
There will be noise during the rocket-powered deceleration, however, so the craft will land 6km or more from urban built-up areas – still close enough for speedy deliveries from the other side of the world.
3. Could this be composites’ steel moment?
Lightweight yet strong, composites have revolutionised aerospace manufacturing. They are still expensive and relatively slow to make, however, owing to manufacturing limitations.
Bristol University spin-out Icomat showed its solution to visitors to the Aerospace Technology Institute’s pavilion. The company’s rapid tow shearing technology uses a robotic system to ‘steer’ composite tapes along curved paths, precisely placing fibres to build parts such as beams, spars and fuselage skins.
“We can steer the fibres to really optimise where you place your material for certain parts, which gives you better structural efficiency and lower weight,” said CEO Dr Evangelos Zympeloudis. “The other big advantage is that it's an automated manufacturing process, so you can produce an order of magnitude faster compared to what you could before.”
The system uses finite element analysis alongside a forming optimisation process, providing the optimal path for each fibre. Once it has been placed, the material is stamped – similar to an automotive stamping line – and the fibres “end up exactly where you want them to be”.
The company recently raised £23m funding from investors including the defence and security-focused Nato Innovation Fund. It has also received “substantial” funding from the UK Space Agency to support opening of the firm’s first factory in Gloucestershire.
The long-term vision is much wider use of composites, said Dr Zympeloudis. “It’s a little bit like a story I really like, Bessemer and Carnegie with steel in the [mid] 1800s. Back then it was a nice exotic material, and they used it to make forks and knives etcetera,” he said.
“Then what Carnegie and Bessemer did is, they did not reinvent steel, they just found a way to make it lighter and to make it cheaper – and that gave us railways, skyscrapers.”
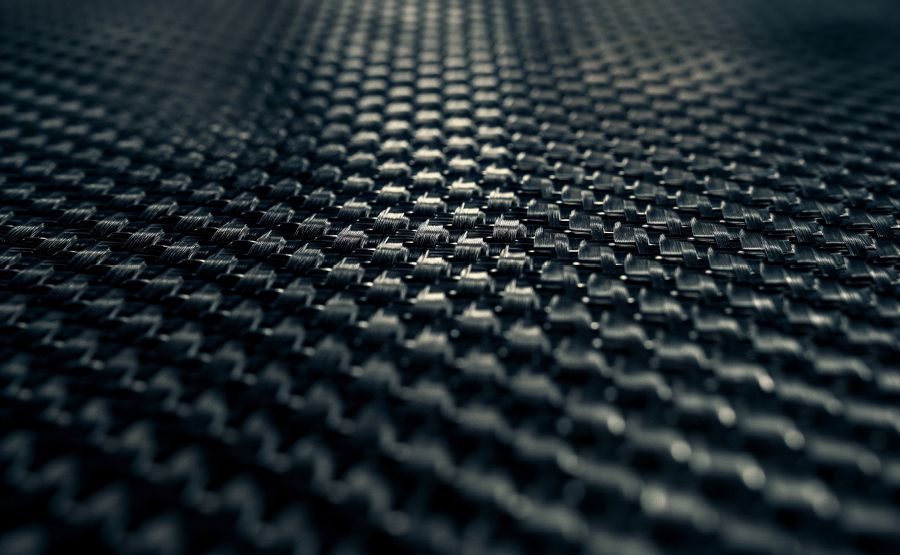
4. Shetland spaceport prepares for launch
Scott Hammond, deputy CEO of SaxaVord Spaceport in Shetland, also appeared in the Space Zone Theatre. The first fully licensed vertical-launch spaceport in Europe, the facility recently ground tested a rocket stage from German manufacturer Rocket Factory Augsburg ahead of a planned orbital test flight this autumn.
“This will be the very first time that an orbital launch, a vertical orbital launch from the United Kingdom has been staged,” Hammond said. “The next step really is to light the blue touchpaper and let the rocket fly up into space.”
If tests go well, the facility aims to provide up to 30 launches each year. “What we're trying to do here is have a repeatable launch capability. We're not just looking at one launch, we are making sure we have all the agreements that allow us to do that,” Hammond said.
Government support will be vital to long-term success, Hammond said, with other countries such as France spending hundreds of millions of pounds on rocket start-ups.
You're reading a brand new digital publication from the team at Professional Engineering, made exclusively for IMechE members and available on all devices. We'd love your feedback: let us know what you think at profeng@thinkpublishing.co.uk